Plastic Injection Molding Service For Custom Parts
High Quality Plastic Parts
Professional DFM Analysis
Production parts as fast as 10-15 days
Dozens of materials and finishes are available
Plastic Injection Molding Service Online Quote
Plastic injection molding is a manufacturing process used to produce large volumes of plastic parts. The injection molding process involves injecting molten plastic material into a mold cavity, where it cools and solidifies into the desired shape. Then eject the molded plastic part. This method is widely used because it can create complex shapes with high precision and consistency, making it ideal for mass production. The injection molding services, in addition to the rapid completion of bulk plastic parts, also have a lower cost of characteristics.
At HordRT, plastic injection molding service is a core service. With over 11 years of experience, we provide on-demand manufacturing from prototype to production. As an injection molding manufacturer, we handle projects of any size or complexity, delivering high-quality parts, competitive pricing, and quick lead times. Andwe have no minimum order.
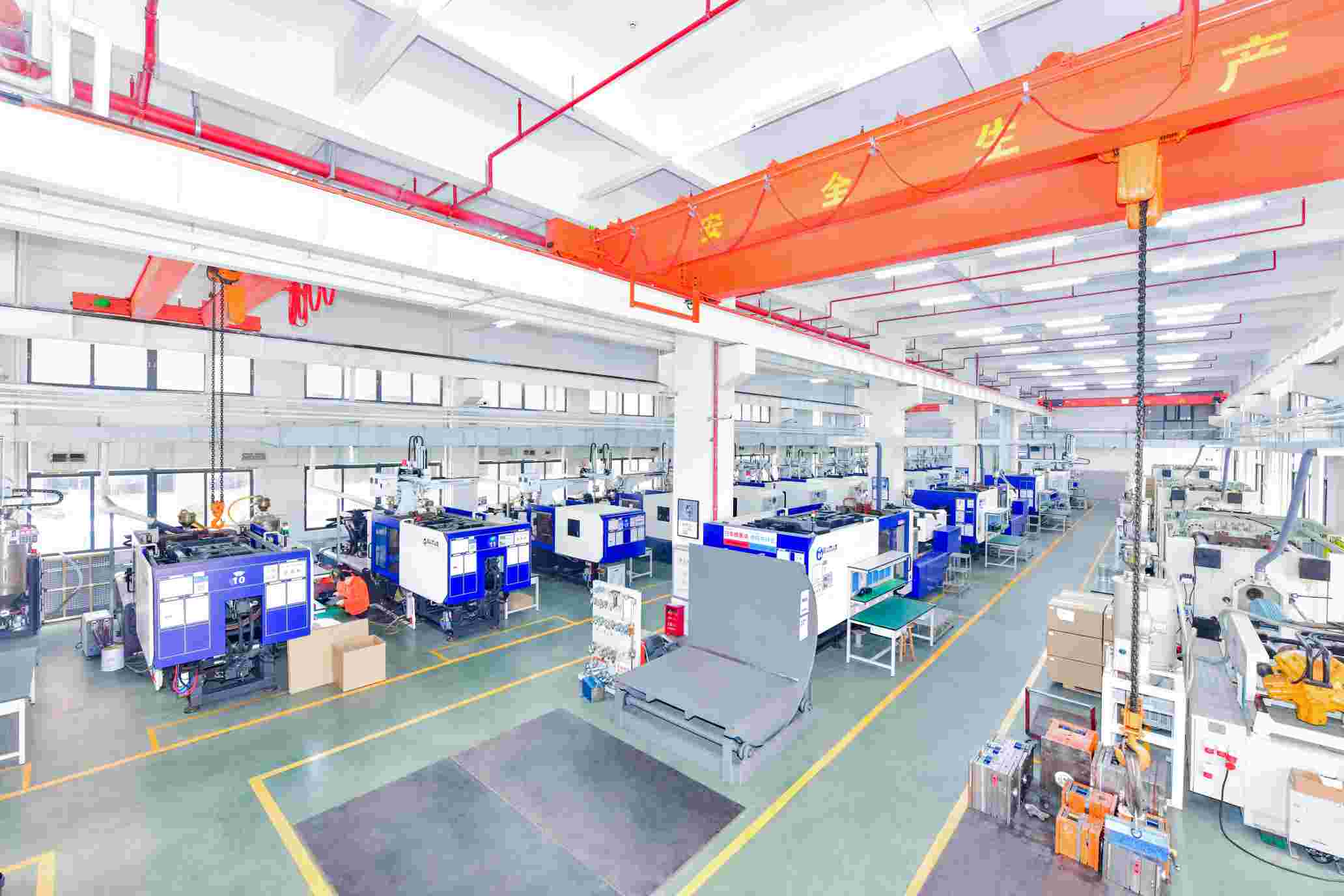
How Custom Plastic Injection Molding Works
Key Steps in Plastic Injection Molding:
- Setting up the mold to the injection molding machine.
- Feeding and melting the thermoplastic
- Injecting the plastic into the mold.
- Holding and Cooling.
- Ejecting and Finishing processes.
The injection molding process can be repeated hundreds or thousands of times rapidly, which helps amortize the cost of tooling and reduces the cost of each unit to just a few dollars or less. At HordRT, our tools may feature a single cavity or hundreds of cavities, allowing for the production of countless parts. The manufacturing cycle varies based on the material, size, and complexity of the part.
Unlock precision and speed with our injection molding services. Efficiently obtain your custom prototype and production molded parts. Submit your design for a free quote today!
Plastic Injection Molding Materials
Our robust supply chain ensures that we source the highest-quality materials for your project. We work directly with manufacturers and their authorized agents to provide you with top-grade injection molding materials, accompanied by detailed technical datasheets for each. This approach helps prevent potential issues related to material sourcing. For standard applications, we recommend our stock materials, which are both cost-effective and efficient. However, if your project requires specialized materials, we can accommodate those needs to meet your exact specifications.
The following materials are the most commonly used for plastic injection molding:
Get our injection molding materials list available. please check and confirm with our project manager if your expected material is not in the list.
Available Surface Finishes for Injection Molding
As a leading global molding manufacturer with 20 years of industry experience, we have the expertise to provide custom injection molding services tailored to your product needs. We offer various surface finish options for plastic parts, ensuring the final product meets your exact specifications. If you have any additional surface finish requirements, please feel free to contact us.
- As Molded
- SPI Finishes
- Polishing
- Silk screening
- Pad printing
- Glossy
- Matte
- Painting
- Etching
- Laser Engraving
- CustomFinishing
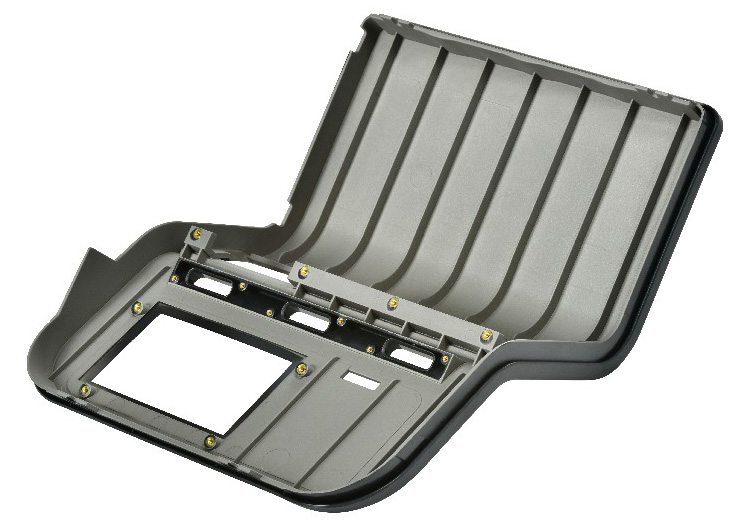
HordRT Injection Mold Classes
We produce injection molding tooling mainly from aluminum or tool steel. Currently, our molds are more suitable for the manufacture of law-volume manufacturing of rapid injection molding parts. The injection molding tooling complies with the SPI mold classification.
SPI Mold Classification | Cycle Count | Description |
101 | 1,000,000 or more. | HordRT 101-grade steel molds are designed for over 1,000,000 cycles. Made from premium materials, these Class I molds are perfect for multi-cavity structures, and prototype production. |
102 | Up to 1,000,000. | HordRT 102-grade steel molds are ideal for medium to high production volumes and parts requiring close tolerances, especially with abrasive materials. Known for high quality and reasonable pricing, these Class II tools meet the demands of large-scale part production. |
103 | Up to 500,000. | Designed for up to 500,000 cycles, HordRT Grade 103 steel molds are ideally suited for low to medium production needs and offer excellent value in the general price range. Also known as Class III tools, they are reliable and durable for a variety of manufacturing applications. |
104 | Up to 100,000. | HordRT 104-grade steel molds are designed for up to 100,000 cycles, ideal for low production volumes and non-abrasive materials. Known as Class IV tools, they offer a cost-effective solution within a low to moderate price range. This is basically the injection molding tooling of choice for producing parts in small production runs. |
105 | Up to 500. | HordRT 105-grade steel molds are designed for up to 500 cycles, specifically for prototype production. Constructed with a focus on cost-effectiveness, these molds are ideal for producing a small quantity of prototype parts. Known as Class V tools. |
Benefits of Injection Molding Service
Injection molding is the fastest and most cost-effective way of manufacturing hundreds and thousands of finished plastic parts. And it is one of the most popular businesses in our company. There are lots of advantages of rapid injection molding.

Fast production and highly efficient
The injection molding process is highly efficient, which can produce an incredible amount of parts per hour.

A large number of materials are available
There is a wide range of materials available. Ability to use multiple plastic materials simultaneously. Commonly used materials include acrylonitrile butadiene styrene (ABS), polyethylene (PE), polystyrene (PS), and polypropylene (PP).

Scalability and repeatability
One of the main benefits of plastic injection molding is its high repeatability. An aluminum mold will generally last between 5,000 and 10,000 cycles, and a full-scale steel production mold can last for over 100,000 cycles.

Cost-effective
The injection molding process is repeated hundreds or thousand of times quickly, which an amortize the cost of tooling and reduce the cost of each unit to a few dollars or less.
Common Applications
Injection molding is widely used across various industries. Our expert team delivers production solutions to help bring your products to market faster.

Medical devices and Dental

Automotive

Aerospace

Electronics

Consumer Products

Energy
Addition Injection Molding Options
In addition to the basic injection molding service, we also provide Over-molding and Insert Molding.
Over-molding
Over-molding, also known as two-shot, multiple-material molding, two-shot, or 2k molding, is a unique custom injection molding process that combines multiple materials seamlessly into a single part or product. It typically includes a rigid, plastic-base component overlaid with a thin, pliable, rubber-like thermoplastic elastomer (TPE) exterior layer or other materials using either a single-shot (insert molding) or two-shot (multiple-shot molding) technique. The over-molding process may be an excellent option for your next project after considering its significant advantages.
Insert Molding
Insert molding, also known as metal insert molding or plastic insert molding, is commonly used to add metal parts to injection molded parts during molding rather than after the parts have cured, cutting down on post-molding manufacturing/assembly operations.
Insert Molding
WHY CHOOSE US
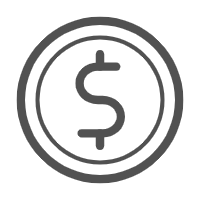
INSTANT QUOTING
Timely reply and provide the quote within 24 hours

NO MOQ REQUIRED
Hord does not have minimum order quantity
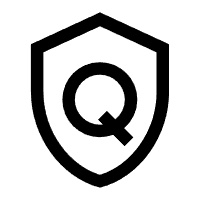
HIGH QUALITY
ISO 9001 & IATF 16949 certificated and inspect every step
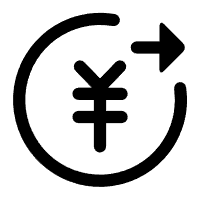
COST-EFFICIENT
+30% cost lower than western competitors
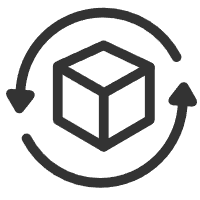
QUICK TUAROUND
Parts make in 7 days and delivery on time
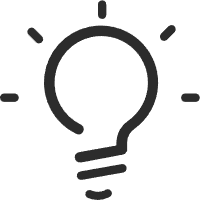
DFM ANALYSIS
Once receiving the inquiry, we will provide you with a preliminary DFM report
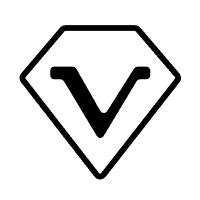
PROFESSIONAL SERVICES
More than 20 years of rapid tooling making
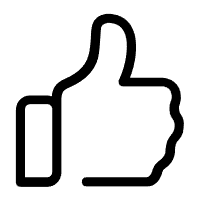
GOOD RAPUTATION FROM CUSTOMERS
Customers are satisfied with our services, products quality and delivery time.
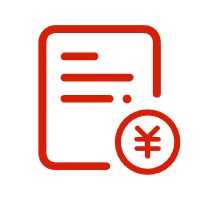

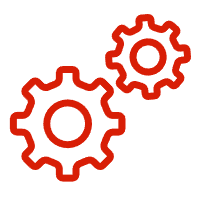
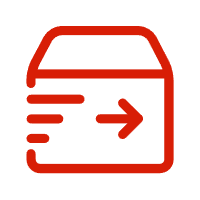
Injection Molding FAQs
To place an order, you will need to provide your part design, material specifications, quantity, and any additional requirements such as finishing or color. After reviewing your order, we will provide a quote and production timeline. Once confirmed, we will begin the manufacturing process.
When selecting a plastic material, you should consider factors such as strength, flexibility, temperature resistance, and chemical resistance, depending on the part’s intended use. Our team can guide you in choosing the best material for your application.
Yes, we offer rapid prototyping services using injection molding. We can produce small quantities of prototypes to verify your design before committing to full-scale production.
The lead time for mold creation typically ranges from 1 to 2 weeks, depending on the complexity of the mold design. We can provide a more accurate timeline after reviewing your specific requirements.
We can use a wide range of thermoplastic and thermosetting materials, including but not limited to ABS, PP, PS, PE, PC, Nylon, POM, PVC, and silicone. We also provide services for custom materials upon request.

Cases of Plastic Injection Molding
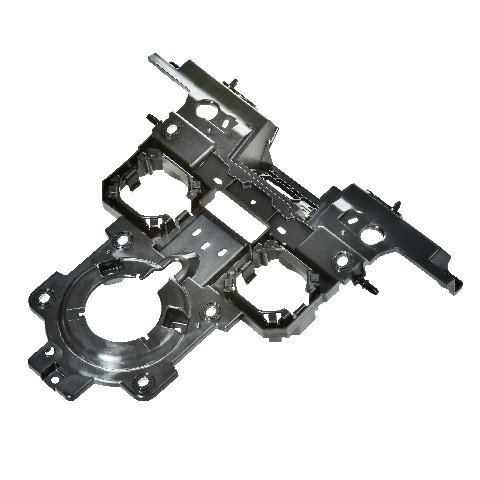


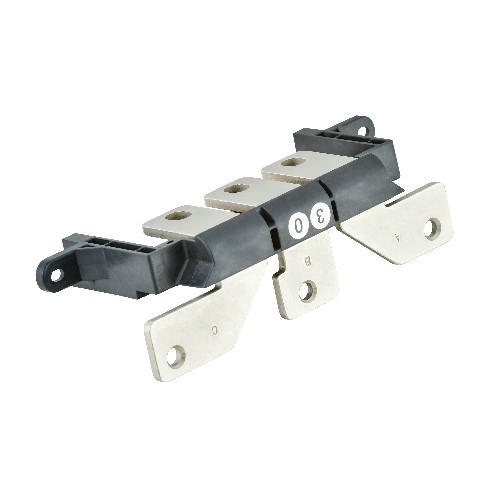

Let us help you provide high quality parts in short time. Get your project started now!
Caution: HordRT is full Chinese company, please don't send any enquiry items involved export controlled by U.S. law. e.g. EAR, ITAR etc
Injection Molding Resources

Top 4 Reasons Why Choose HordRT as Your Trusted Injection Molding Manufacturer
HordRT, an injection molding manufacturer, stand out as a reliable and reputable supplier of rapid injection molding. Let's delve into why injection molding has
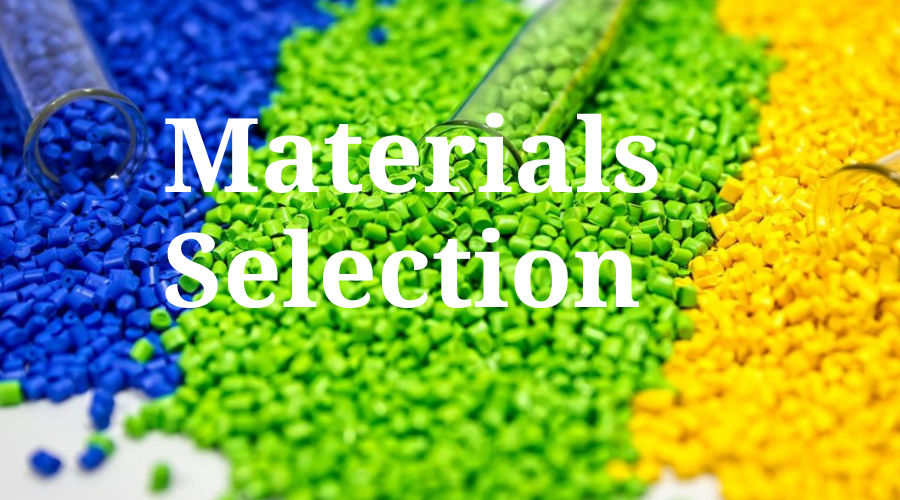
Material Selection and Design Principles in Injection Molding
The art of injection molding has revolutionized the manufacturing industry, enabling the creation of complex and intricate products with unmatched precision and efficiency. From consumer

Common Plastic Injection Molding Defects and Solutions: A Comprehensive Guide
Plastic injection molding is a widely used manufacturing process for producing plastic parts. However, it is not without its challenges, and defects can occur during