The art of injection molding has revolutionized the manufacturing industry, enabling the creation of complex and intricate products with unmatched precision and efficiency. From consumer goods to automotive components and medical devices, injection molding has become the cornerstone of modern production processes. However, achieving impeccable results in injection molding requires more than just advanced machinery and skilled technicians. At the heart of every successful injection molding endeavor lies the critical interplay between material selection and design principles. In this article, we will explore commonly used materials in injection molding processes and the key factors to consider during the material selection and product design, including strength, heat resistance, and cost.
1. Material Selection in Injection Molding
The selection of suitable materials is crucial for achieving desired part characteristics and meeting application requirements. Some commonly used materials in injection molding include:
- Thermoplastics: Versatile and wide used, thermoplastics such as polyethylene(PE), polypropylene(PP), and polystyrene(PS) offer excellent durability, chemical resistance, and processability.
- Engineering Plastic: Materials like acrylonitrile butadiene styrene (ABS), polycarbonate(PC), and nylon(PA) exhibit enhanced mechanical properties, heat resistance, and dimensional stability, making them suitable for demanding applications.
- Elastomers: Elastomeric materials, including thermoplastic elastomers(TPE) and thermoset rubbers, provide elasticity and flexibility for applications requiring rubber-like characteristics.
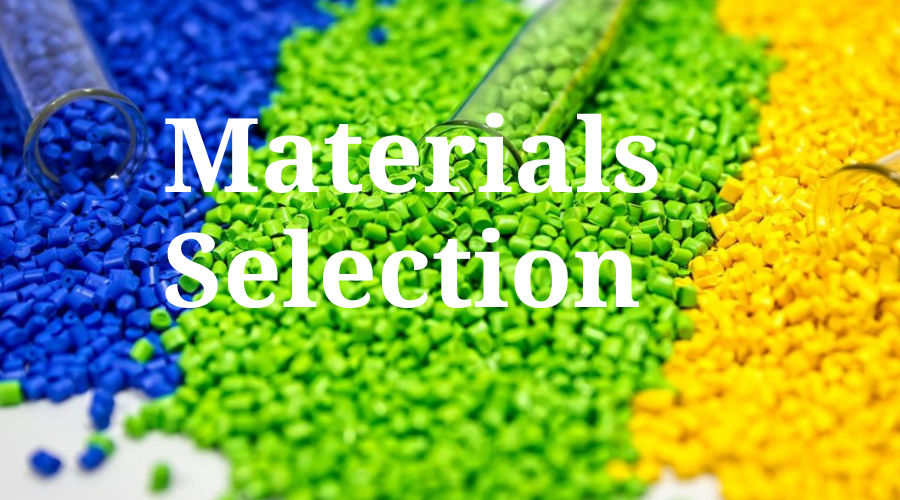
2. Factors to Consider in Material Selection
- Mechanical Strength: Consider the mechanical properties required for the part, including tensile strength, impact resistance, and flexural modulus. The material should withstand the intended loads and stress levels.
- Heat Resistance: Evaluate the operating temperature range and any thermal stress the part may encounter. Choose materials with appropriate heat resistance to maintain dimensional stability and prevent deformation.
- Chemical Compatibility: Consider the exposure to chemicals, solvents, or environmental factors that the part may experience. Select materials resistant to corrosion or degradation caused by specific substances.
- Electrical Properties: Asses the electrical conductivity or insulating properties needed for the application. Certain materials offer excellent electrical insulation, while others provide conductivity for specific applications.
- Appearance and Aesthetics: Consider the desired surface finish, color options, and transparency requirements for the part. Some materials offer enhanced aesthetics and can be easily colored or made transparent.
- Cost-effectiveness: Balance material cost with performance requirements and production volumes. Optimize material selection to achieve the desired functionality while minimizing manufacturing costs.

Design Principles for Injection Molding
Apart from material selection, design principles play a crucial role in achieving successful injection molding:
Wall Thickness: Maintain uniform wall thickness to ensure proper flow and minimize issues like sink marks or warpage. Thick sections take longer to cool, while thin areas may cause flow restrictions or structural weaknesses.
Draft Angles: Incorporate draft angles on vertical surfaces to facilitate easy ejection from the mold. Adequate draft angles prevent part sticking and reduce the risk of damage during demolding.
Rib Design: Use ribs to improve past stiffness without significantly increasing material usage. Proper rib design enhances structural integrity and reduces the likelihood of deformation or warpage.
Parting Line and Ejector Pin Placement: Determine the parting line and ejector pin locations to achieve smooth part ejection and minimize visible parting line marks.
Conclusion
Material selection and design principles are critical factors in the success of injection molding projects. By considering the specific requirements of the application and evaluating factors such as strength, heat resistance, and cost, designers can identify suitable materials. Concurrently, adherence to design principles ensures proper part functionality, dimensional accuracy, and ease of manufacturing. By mastering material selection and design principles in injection molding, manufacturers can produce high-quality parts that meet performance demands, reduce costs, and enhance overall customer satisfaction.