Contents
Sheet metal fabrication is a crucial process in various industries, from automotive and aerospace to construction and electronics. However, it can also be a significant expense. Finding ways to reduce costs without compromising quality is essential for staying competitive in today’s market. In this article, we’ll explore top tips for minimizing sheet metal fabrication costs while maintaining the desired standards.
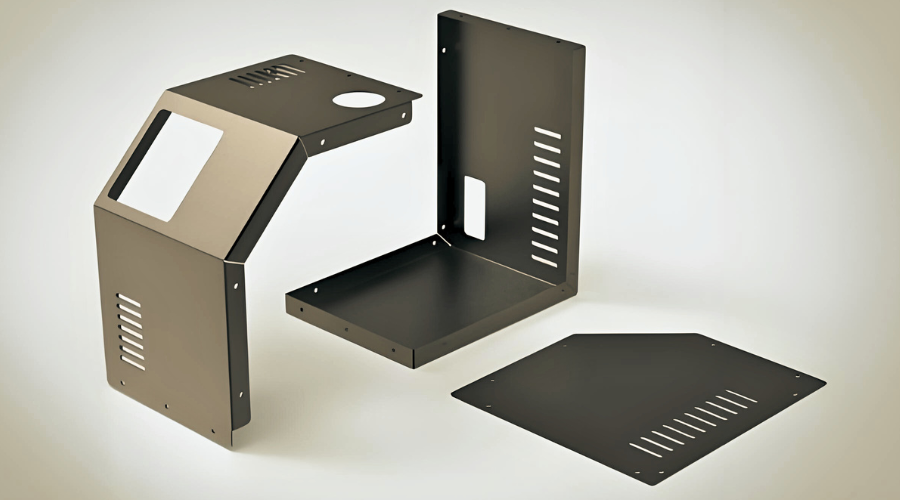
1. Design for Manufacturability (DFM)
Design for manufacturability (DFM) is a critical concept that emphasizes designing products in a way that simplifies manufacturing processes and reduces costs. By considering fabrication constraints during the design phase, you can avoid costly redesigns and production delays. Here are some DFM principles to keep in mind:
- Simplify Designs: Minimize complex features and unnecessary details that increase machining time and material waste.
- Standardize Parts: Use standard sizes and shapes whenever possible to reduce customization costs.
- Optimize Material Use: Design parts to maximize material usage, reducing scrap and lowering mate
2. Choose the Right Materials
Selecting the appropriate material for your sheet metal project can significantly impact costs. While it might be tempting to opt for the cheapest material, consider the following factors:
- Material Properties:Ensure the material meets the required strength, durability, and corrosion resistance.
- Availability:Choose materials that are readily available to avoid delays and high procurement costs.
- Processing Costs: Some materials are easier and cheaper to work with. For example, aluminum is often more cost-effective to machine than stainless steel.
3. Leverage Advanced Technology
Investing in advanced fabrication technologies can lead to long-term savings by improving efficiency and reducing waste. Consider the following technologies:
- Laser Cutting:Provides high precision with minimal material waste, especially for complex shapes.
- Automated Bending:Reduces labor costs and increase accuracy for bending operations.
- CNC Machining:Offers consistent, high-quality parts with reduced setup times and lower labor costs.
4. Optimize Production Processes
Streamlining production processes can result in significant cost savings. Here are some strategies to optimize your workflow:
- Batch Processing:Group similar parts together to minimize setup times and increase throughput.
- Lean Manufacturing:Implement lean principles to eliminate waste, improve quality, and reduce costs. This includes practices like 5S, continuous improvement, and just-in-time production.
- Regular Maintenance:Keep your equipment in top condition to avoid downtime and costly repairs.
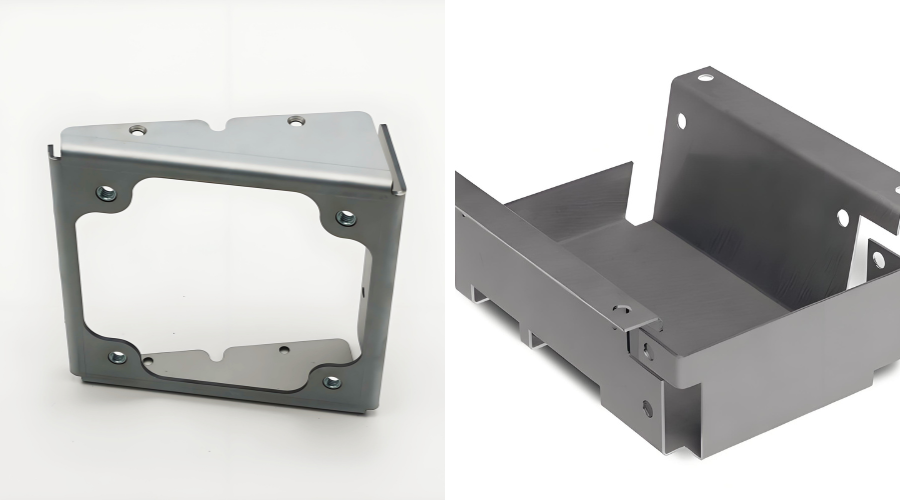
5. Improve Material Utilization
Efficient material utilization is essential for cost-effective sheet metal fabrication. Here are some ways to reduce material waste:
- Nesting Software: Use nesting software to optimize the arrangement of parts on the sheet, maximizing material usage and minimizing scarp.
- Remnant Utilization:Develop a system for tracking and using remnant materials in future projects.
6. Collaborate with Your Fabricator
Working closely with your sheet metal fabricator can uncover opportunities for cost savings. Open communication can lead to better design decisions and process improvements. Consider the following:
- Early Involvement:Involve your fabricator early in the design process to identify potential issues and cost-saving opportunities
- Regular Feedback:Establish a feedback loop with your fabrication to continually improve designs and processes based on real-world performance.
Conclusion
Optimizing sheet metal fabrication costs requires a holistic approach that considers design, material selection, technology, and process efficiency. By implementing these expert tips, manufacturers can achieve significant savings while maintaining high-quality standards. Remember, the key to successful cost optimization is continuous improvement and collaboration with your fabricator. Embrace these strategies to stay competitive in the dynamic manufacturing landscape.
For more insights and personalized advice on optimizing your sheet metal fabrication processes, contact our experts at HordRT. We’re here to help you achieve efficiency and savings in every project.
Ready to take your sheet metal fabrication to the next level? Reach out to us today and discover how our advanced technologies and expert team can transform your manufacturing process.