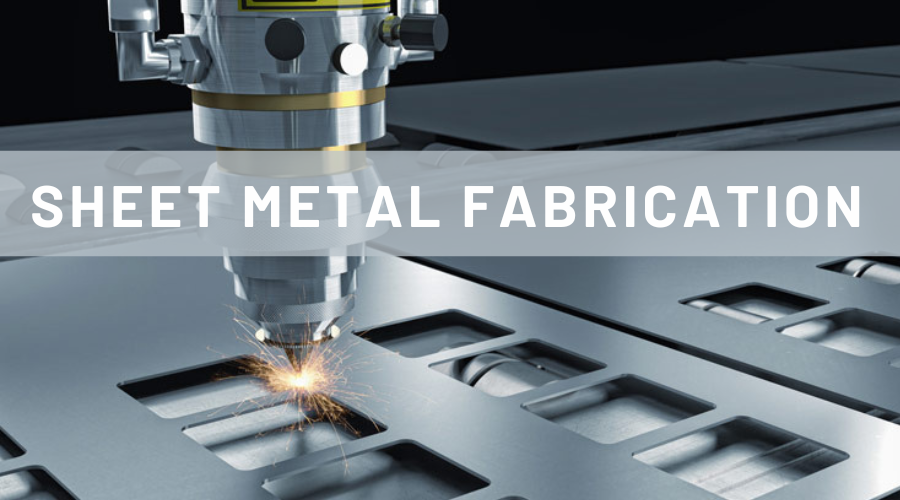
Sheet metal fabrication is a versatile and precise manufacturing process that involves transforming flat metal sheets into various useful products. It encompasses a wide range of techniques, including cutting, bending, welding, and finishing. Sheet metal fabrication has revolutionized industries such as construction, automotive, aerospace, and manufacturing by enabling the creation of complex, customized, and durable metal components. This article explores the art and science of sheet metal fabrication, its processes, applications, and its impact on various sectors.
The Fundamentals of Sheet Metal Fabrication
Sheet metal fabrication begins with the selection of suitable metal sheets, such as steel, aluminum, copper, or stainless steel. These sheets are available in various thicknesses, referred to as gauges. Thinner gauges are flexible and malleable, while thicker gauges offer greater strength and rigidity.
Cutting Processes
Cutting is the initial step in sheet metal fabrication, and several techniques are employed:
Shearing: A guillotine-like tool cuts the metal along a straight line, allowing for precise and efficient cuts.
Laser Cutting: Utilizing a high-powered laser beam, intricate and complex shapes can be cut with exceptional accuracy.
Waterjet Cutting: High-pressure water mixed with an abrasive material is used to cut through the metal, offering versatility and minimal heat-affected zones.
Plasma Cutting: A plasma torch generates a high-temperature plasma arc that melts the metal, allowing for efficient cutting.
Forming and Bending Processes
Press Brake Bending: A press brake machine applies force to the metal sheet, bending it to the desired angle. This process creates various shapes, such as U-bends, V-bends, and complex curves.
Roll Forming: Continuous bending of the metal sheet using a series of rollers to create long sections with consistent shapes.
Stamping: A mechanical or hydraulic press is used to deform the sheet metal into a specific shape or pattern, often used for mass production of identical parts.
Joining Processes
Joining methods are employed to assemble multiple sheet metal components into a single structure:
Welding: Common welding techniques such as MIG (Metal Inert Gas), TIG (Tungsten Inert Gas), and spot welding are used to fuse metal sheets together, providing robust and permanent joints.
Fasteners: Rivets, screws, and bolts are utilized to secure metal sheets in place, offering ease of disassembly and reassembly.
Adhesives: Specialized adhesives designed for metal bonding can be employed to join sheets, providing a clean and seamless appearance.
Finishing Processes
Finishing touches enhance the appearance and functionality of fabricated sheet metal products:
Deburring: Removing sharp edges and burrs to ensure safety and improve aesthetics.
Grinding and Sanding: Smoothing and refining the metal surface for a polished finish.
Surface Treatment: Applying paint, powder coating, anodizing, or plating to protect against corrosion, enhance durability, and improve aesthetics.
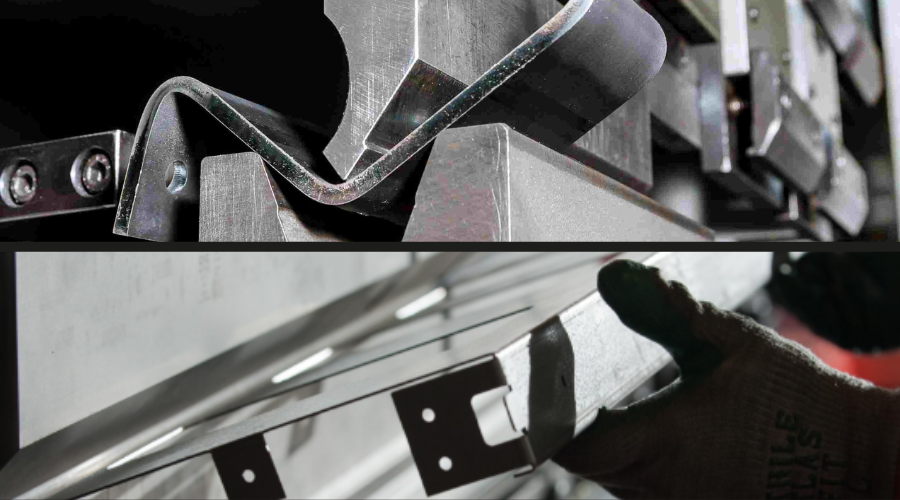
Applications of Sheet Metal Fabrication:
Sheet metal fabrication finds widespread application across various industries:
Construction and Architecture: Roofing, facades, staircases, and structural components.
Automotive and Transportation: Body panels, frames, exhaust systems, and engine components.
Aerospace and Aviation: Aircraft structures, wings, fuselages, and interior fittings.
Electronics and Appliances: Enclosures, cabinets, electrical panels, and appliance components.
Industrial and Manufacturing: Machinery components, storage systems, and material handling equipment.
Art and Design: Sculptures, decorative elements, and architectural features.
Advantages and Limitations of Sheet Metal Fabrication:
Sheet metal fabrication offers several advantages:
Strength and Durability: Fabricated metal components exhibit high strength and can withstand harsh environments.
Customization and Precision: Sheet metal can be shaped into intricate designs and precise dimensions, meeting specific requirements.
Cost-effectiveness: Efficient production processes, material optimization, and recyclability contribute to cost savings.
High Production Efficiency: Mass production techniques and automated processes enable quick and large-scale fabrication.
However, sheet metal fabrication also has limitations:
Material Constraints: The choice of materials is limited to those that are available in sheet form.
Design Constraints: Complex and irregular shapes may pose challenges in fabrication.
Tooling and Setup Requirements: Specialized equipment and tooling may be necessary for certain processes.
Conclusion
Sheet metal fabrication is a transformative process that allows raw metal sheets to be crafted into intricate and functional products across diverse industries. The combination of cutting-edge technology, skilled craftsmanship, and innovative design possibilities has revolutionized the manufacturing landscape. As sheet metal fabrication continues to evolve, it remains a driving force behind the creation of durable, efficient, and aesthetically pleasing metal components that shape our world.
Our sheet metal fabrication services offer a wide range of possibilities for your project. Whether you require custom components for architectural designs, automotive parts, aerospace structures, or industrial machinery, we have the expertise and capabilities to bring your ideas to life. Our skilled craftsmen and cutting-edge technology ensure precision and accuracy in every step of the fabrication process. From cutting and forming to welding and finishing, we pay meticulous attention to detail to deliver high-quality results. With our commitment to innovation and customer satisfaction, we strive to exceed your expectations and provide you with durable, functional, and aesthetically pleasing sheet metal solutions. Partner with us for your sheet metal fabrication needs and experience the seamless integration of craftsmanship, technology, and creativity. Contact us now!