Contents
CNC is a type of process that has wholly redesigned manufacturing processes by computer programs, providing the user with vital control of machine tools that come with high precision. Recent emphasis has been focused on developing high-speed CNC machining as a form of procedure for its ability to increase productivity and quality within the CNC machining industry.
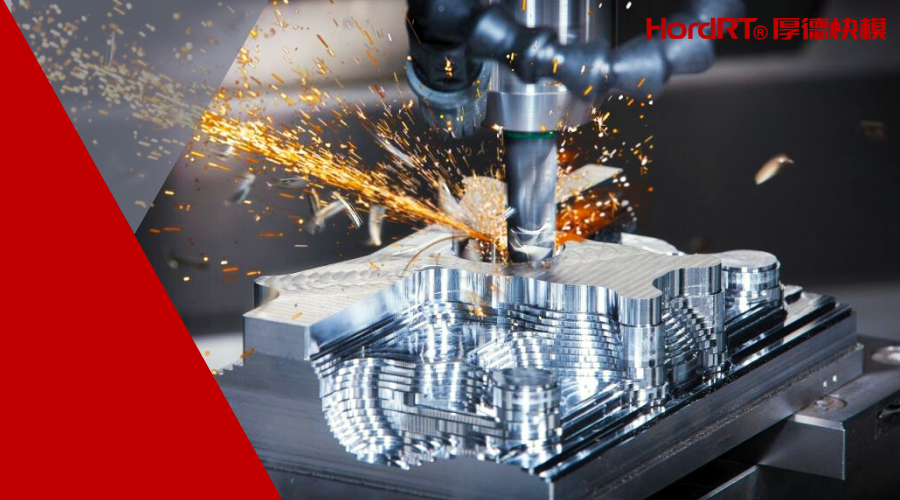
What is High-Speed CNC Maching
High-speed CNC machining is the process of machine tools running at very high rates compared to conventional ones. High-speed CNC means applying new technologies to increase significantly the rotation speed of the spindle, the advancement speed, and the cutting speed.
It should ensure that heat in high-speed CNC machining is appropriately managed. Schemes used for cooling and heat treatment ensure that tools are not overheating, hence leading to more extended tool and material life. An example is the advanced cooling system through its spindle coolant delivery and high-pressure air jets.
Benefits of High-Speed CNC Machining
High-speed CNC machining realizes the following benefits: cutting down respective production times, which makes it the most preferred way in most modern manufacturing processes:
1. Increased Productivity and Efficiency
Speed is one of the critical advantages of using CNC machining, as it allows the making of many products within a short time frame, increasing production. If the speed is high, it implies that more parts would be produced within a concise duration, something that would generally impact the efficiencies of machining.
2. Better Accuracy and Precision
The CNC machinery is designed with precision and accuracy to super-high rates at incredible speeds. The industry requires such precision in the making of machinery, for example, aerospace, medical devices, and the like, where the tolerances are small.
3. Tremendously Improved Production Speeds and Shortened Cycle Times
CNC machining can work at high speeds, making it possible to have high real-potential production rates. These high rates result from small cycle times; therefore, this plays a vital role in beating tight deadlines and increasing the output.
4. Smoother Surface Finish and Minimal Post-Processing
High-speed CNC machining, therefore, is to be done with an improved surface finish, which reduces the need for further elaborate post-finishing methods. That would save valuable time in the first place, and other expenses now have to be borne for further treatment of finishing work.
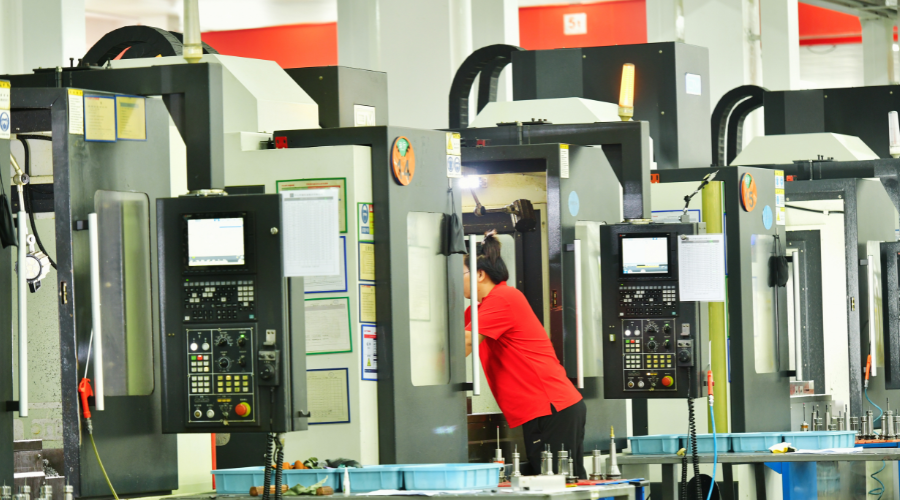
High-Speed CNC Machining Application
High-speed CNC machining is a highly productive and versatile manufacturing process with diversified applications in many industries. Some of the sectors in which it is widely applied include:
1. Car Industry
The auto industry employs high-speed CNC machining for manufacturing building elements of the engine, transmission, and other critical parts that have to be both precise and hardly.
2.Aerospace and Defense
High-speed CNC machining makes secure and efficient production possible, even for the most complex aerospace and defense sector elements, from turbine blades to wide-spanning structural components and complex assemblies.
3. Electronic and Semiconductor Manufacturing
High-speed CNC machining is a driving process, especially in the electronic and semiconductor manufacturing industries. The precision parts machined within this process can attain tight tolerances in small detailed sizes, hence translated into functionality in the respective electronic gadgets.
4. Medical Device Manufacturing
"In the medical field, precision is everything." The high-speed CNCs are utilized to create surgical equipment, implants, and other medical devices that conform to exact specifications to work toward high-style finishes.
5. Tool and Die Making
High-speed CNC machining is very valuable to the tool and dies industry, as the process it carries out yields very accurate molds and dies, which are in turn applied in most manufacturing processes.
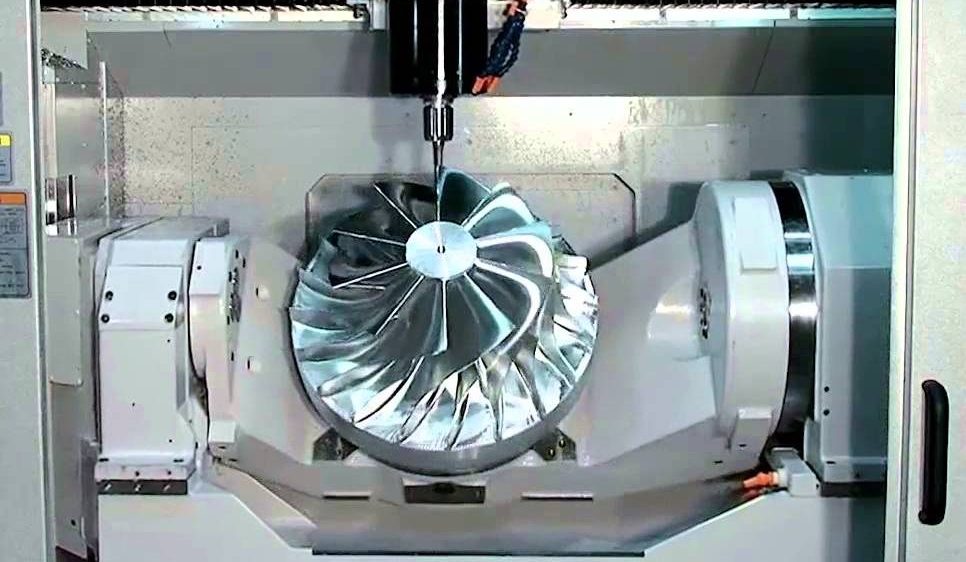
Challenges and Solutions of High-Speed CNC Machining
With all the advantages associated with high-speed CNC machining, it is plagued by disadvantages. Then, it becomes essential to understand when to apply the techinique.
1. Managing of Heat and Tool Wear
The high temperature developed at the high speeds causes the tool to wear out and also leads to material deformation. These issues are resolved by employing better cooling techniques and high-qaulity cutting tools.
2. Vibration and Stability Problems
The significant problems of high-speed machining include cutting forces, die vibration, and stability. Vibration and stability in machine structure rigidity, along with proper vibration technologies, should improve necessarily.
3. Material-Specific Problems and Solutions
High-speed machining reacts differently to the various materials being worked on. The material in use requires the customizing of the machining process in line with the designing speeds and tools, feeds, and methods of cooling.
4. Integration with Current Operations of Manufacturing
High-speed CNC machining depends on the previous ways of manufacturing. The process must be, therefore, highly compatible and seamlessly operate in proper planning and co-ordination of activities.
Conclusion
High-speed CNC sets entirely new standards in productivity, precision, and efficiency in the manufacturing arena. Of course, challenges always tag along with it, but compared to the benefits, they are minuscule. The knowledge of and meeting these challenges equip the manufacturer to easily avail himself of the enormous srt of benefits placed on the table by high-speed CNC machining.
If your're looking explore rapid CNC machining further, consider the expertise of HordRT.