In injection molding, material selection is important in determining the final product's performance, durability, and suitability for its intended application. This is especially true in high-temperature environments where materials must withstand elevated temperatures without degrading, warping, or losing their mechanical properties. Heat-resistant injection molding materials are essential for ensuring long-term reliability and functionality.
In this article, we will explore the types of injection molding materials suitable for high-temperature applications and provide insights into how to choose the right material for your project.

Material Categories and Performance Comparison
The categories below are broadly classified based on their temperature tolerance and mechanical performance.
1. General-Purpose Materials
General-purpose plastics are designed for use in low to medium temperature environments. These materials are cost-effective, versatile, and easy to process, but they may not offer the thermal stability required for high-temperature applications.
- ABS (Acrylonitrile Butadiene Styrene): ABS is commonly used for consumer electronics, automotive components, and toys. It has good strength and impact resistance but typically operates well at temperatures up to 80°C to 100°C (176°F to 212°F).
- TPU (Thermoplastic Polyurethane): Known for its flexibility, wear resistance, and low-temperature toughness, TPU is used in applications like seals, gaskets, and medical devices. However, its temperature resistance typically ranges from 70°C to 90°C (158°F to 194°F).
- PP (Polypropylene): Polypropylene is lightweight and resistant to moisture and chemicals but can only withstand temperatures up to 100°C to 120°C (212°F to 248°F), making it suitable for non-critical applications.
2. Engineering-Grade Materials
For applications that require better thermal performance and mechanical strength, engineering-grade materials are a better choice. These materials can handle medium to high temperatures and offer better durability compared to general-purpose plastics.
- PC (Polycarbonate): Polycarbonate offers excellent impact resistance and transparency, making it ideal for applications like electrical components, automotive headlamp lenses, and medical devices. It performs well at temperatures up to 120°C to 130°C (248°F to 266°F).
- POM (Polyoxymethylene, or Acetal): Known for its high rigidity and low friction, POM is used in gears, bearings, and other moving parts. It has good resistance to higher temperatures, typically up to 130°C to 150°C (266°F to 302°F).
- PA66 (Polyamide 66): PA66, also known as Nylon 66, is a high-strength thermoplastic used in automotive and electrical applications. It withstands temperatures up to 160°C (320°F), making it ideal for parts subject to higher heat stress.
3. High-Performance Materials
High-performance plastics are engineered to perform in extreme temperature conditions. These materials are essential for industries like aerospace, automotive, and heavy-duty manufacturing, where plastics need to maintain their properties at high temperatures.
- PSU (Polysulfone): PSU is a high-heat resistant plastic that maintains its mechanical properties even at elevated temperatures. It is often used in industrial and medical applications and can withstand temperatures of up to 180°C (356°F).
- PPA (Polyphthalamide): A high-performance material, PPA is used in automotive and electrical applications where exceptional heat resistance and strength are needed. PPA can tolerate temperatures up to 250°C (482°F), making it ideal for extreme conditions.
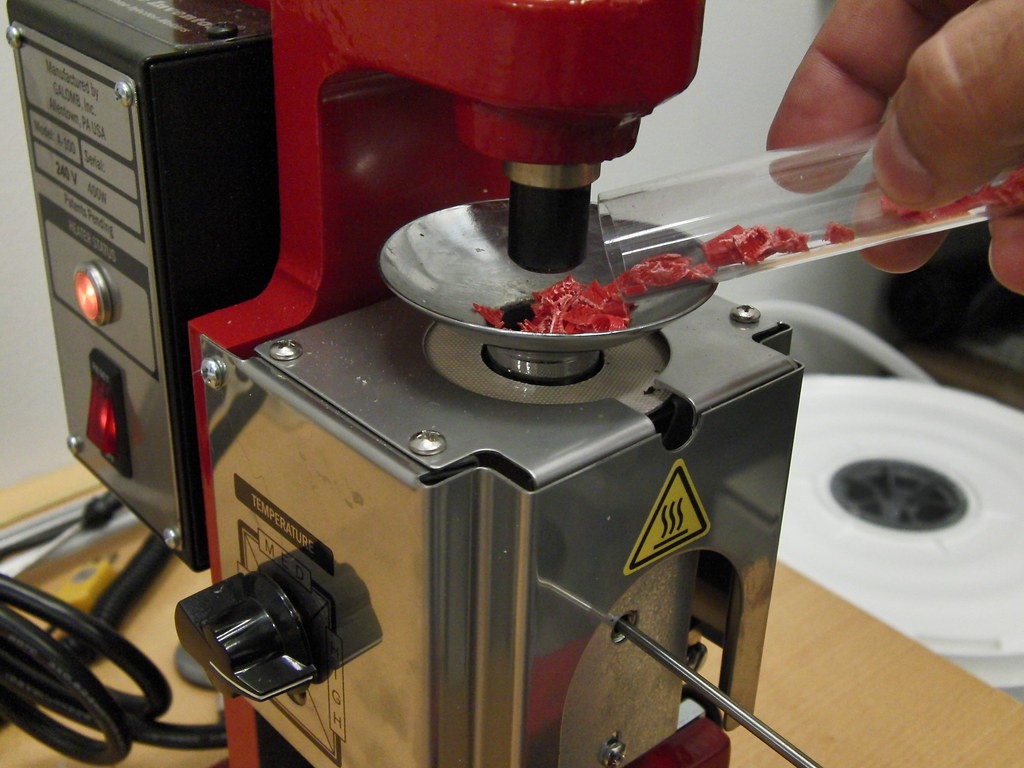
Material Selection Guidelines
Selecting the right injection molding material for a high-temperature application involves several factors. Below are key guidelines to help you choose the appropriate material:
1. Based on Temperature Requirements
For low to medium heat environments, general-purpose plastics like ABS or PP will suffice. For higher temperature resistance, engineering-grade materials like PC or PA66 are more appropriate. For extreme temperature applications, high-performance plastics like PSU or PPA should be considered.
2. Based on Mechanical Performance Needs
Different materials offer varying levels of mechanical strength, rigidity, and impact resistance. For example, if you need a material with high tensile strength and dimensional stability under heat, POM or PA66 are strong candidates. On the other hand, if flexibility is essential, TPU may be more suitable.
3. Based on Chemical Resistance and Environmental Adaptability
If your application will be exposed to chemicals or harsh environmental conditions, it's essential to consider the chemical resistance of the material. High-performance plastics like PSU and PPA offer excellent chemical resistance along with high-temperature tolerance, making them ideal for demanding industrial applications.
Injection Molding Considerations
When molding high-temperature plastics, certain factors must be carefully considered to ensure optimal processing and part quality.
1. Processing Temperatures
Each material has its own optimal processing temperature range. For example, high-performance materials like PPA and PSU may require higher processing temperatures, typically above 300°C (572°F). General-purpose materials like ABS or PP can be processed at lower temperatures, around 200°C (392°F).
2. Mold Design Requirements
High-temperature materials may require specialized mold designs to ensure uniform cooling and prevent warping. The mold material must also be capable of withstanding higher temperatures without degrading.
3. Dimensional Stability and Shrinkage Control
Thermoplastics, especially those used in high-temperature applications, tend to experience more significant shrinkage during cooling. Proper shrinkage control is critical to ensure that parts maintain their dimensional accuracy. Using precise mold designs and understanding the shrinkage rates of each material are vital steps in achieving high-quality injection-molded parts.

HordRT’s Plastic Injection Molding Services
At HordRT, we specialize in providing high-quality plastic injection molding services that cater to industries requiring high-performance materials. Our extensive knowledge of heat moldable plastics and injection molding processes ensures that we can meet your specific needs, whether you are producing automotive parts, medical devices, or high-tech consumer products. With advanced molding technologies, our team can deliver precision-engineered parts that perform well in high-temperature environments.
Conclusion
Selecting the right injection molding material for high-temperature applications is a balancing act between performance requirements and budget constraints. While general-purpose plastics like ABS and PP may suffice for lower heat applications, more demanding projects will require engineering-grade and high-performance plastics such as PA66, PPA, and PSU. Understanding the thermal, mechanical, and chemical requirements of your application is key to making the best material choice.