What is Flash in Injection Molding
In injection molding, “flash” refers to excess material that escapes from the mold cavity during the injection process. When molten plastic is injected into the mold cavity, it can sometimes seep into tiny gaps or spaces between the mold halves, resulting in thins fins or excess material along the edges of the molded part. This excess material is called flash.
While flash may seem like a minor inconvenience, it can lead to significant quality issues and production delays if left unaddressed. In this article, we’ll delve into the top 9 causes of injection molding flash and provide actionable solutions to mitigate them.
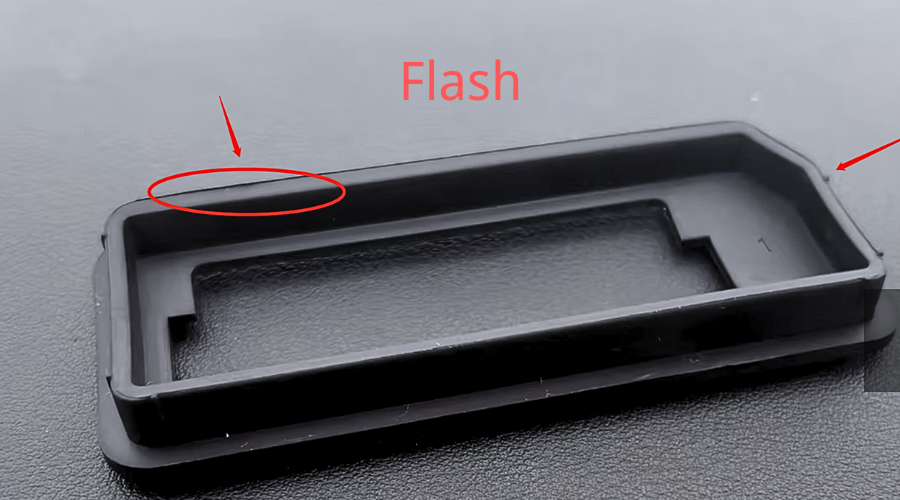
What Cause Injection Molding Flash
- Poor Mold Design or Maintenance: If the mold is not properly designed or maintained, it may not close completely, allowing plastic to seep out during the injection process.
- Excessive Injection Pressure: Using too much injection pressure can force the mold to separate slightly, leading to flash formation.
- Inadequate Clamping Force: If the clamping force is not sufficient to hold the mold halves together tightly during injection, flash may occur.
- Inaccurate Temperature Control: Fluctuations in mold or melt temperatures can affect the viscosity of the plastic, leading to leakage and flash formation.
- Material Issues: The type of plastic used, its viscosity, and additives can all affect how it behaves during the injection process. Some materials are more prone to flash than others.
- Injection Speed: Injection speed that’s too high can lead to increased pressure inside the mold, potentially causing it to separate slightly and allow flash formation.
- Mold Alignment: Misalignment between mold components can result in gaps where plastic can escape, leading to flash.
- Injection Time and Dwell Time: Incorrectly set injection and dwell times can result in excessive plastic being injected into the mold, causing flash.
- Gate Design: Inadequate gate design can lead to excessive pressure buildup, resulting in flash formation.
Effective Ways to Prevent Flash in Injection Molding
Preventing flash in injection molding requires a combination of careful design, precise control of process parameters, and proactive maintenance. Here are some effective ways to prevent flash:
- Optimize Mold Design: Ensure that the mold design is well-suited for the intended part geometry and material. Pay attention to features such as draft angles, venting channels, and gate locations to facilitate smooth material flow and prevent flash formation.
- Maintain Proper Clamp Force: Verify that the mold is securely closed with sufficient clamp force to prevent material leakage during the injection process. Regularly inspect and adjust the clamp force as needed to maintain proper mold closure.
- Ensure Mold Alignment: Align mold components accurately to prevent gaps or misalignment that can allow material to escape and form flash. Conduct routine inspections and maintenance to address any issues with mold alignment promptly.
- Control Injection Pressure: Optimize injection pressure settings based on the material properties and mold design to prevent excessive material flow and minimize the risk of flash formation. Monitor and adjust injection pressure as needed during the molding process.
- Extend Cooling Time: Allow sufficient time for the molded parts to cool and solidify within the mold before ejection. Adjust the cooling time parameters to match the material and part geometry, ensuring complete solidification and minimizing the likelihood of flash.
- Improve Venting: Design the mold with adequate venting channels to allow trapped air or gas to escape during the injection process. Proper venting helps prevent pressure build-up and reduces the risk of flash formation.
- Address Flow Restrictions: Modify the mold design to eliminate narrow flow channels, sharp corners, or other features that could impede material flow and contribute to flash formation. Consider using mold release agents to improve material flow and release.
- Control Temperature Uniformity: Maintain consistent mold temperatures throughout the injection process to ensure uniform material viscosity and filling. Use cooling or heating systems to regulate mold temperature and minimize temperature fluctuations that can lead to flash.
- Regular Maintenance and Inspection: Implement a comprehensive maintenance program to keep the mold and machine components in optimal condition. Conduct routine inspections to identify and address any signs of wear, damage, or degradation that could compromise mold integrity and contribute to flash formation.
- Implement Process Monitoring and Control: Utilize advanced monitoring systems to track key process parameters such as temperature, pressure, and cycle time in real-time. Implement closed-loop systems to automatically adjust process settings and minimize variations that could lead to flash.
Conclusion
By implementing these preventive measures and adopting a proactive approach to mold design, process optimization, and maintenance, manufacturers can significantly reduce the occurrence of flash in injection molding processes, ensuring the production of high-quality molded parts with minimal defects.