When working with complex designs, low-volume rapid CNC machining is a vital tool in modern product manufacturing. The complexity of modern product designs calls for accuracy and precision. Traditional high-volume production is efficient but often requires significant upfront investments in tooling, molds, and setup, which can be expensive for many businesses.
This is where low-volume CNC machining provides a cost-effective substitute that drastically lowers up-front costs. Additionally, it offers the adaptability to quickly alter designs during testing, validation, or customization phases. Low-volume rapid CNC machining is a valuable resource in today's dynamic manufacturing environment due to its adaptability, which enables businesses to fine-tune their products without the limitations of high-volume production.
Benefits of Low-Volume CNC Machining
Businesses can opt for integrating rapid CNC machining in specific situations to enjoy its benefits. Here are the key advantages of low-volume CNC machining.
1. High Efficiency and Cost-Effectiveness
One of the most significant advantages of low-volume CNC machining is its efficiency and cost-effectiveness. Unlike high-volume production, which demands large-scale tooling and setup, low-volume CNC machining reduces upfront costs dramatically. This means businesses can bring their ideas to life without the burden of hefty initial investments.
2. Reduced Lead Times
Low-volume CNC machining also excels in reducing lead times. Previously used manufacturing processes often involved long setup times, delaying production significantly. With low-volume CNC machining, setup is quicker and more flexible, allowing for faster production and quicker time-to-market for new products.

3. Wide Range of Compatible Materials
Another advantage is the ability to work with a wide range of materials. Low-volume CNC machining can operate various materials, from plastics and metals to composites and more. This flexibility allows businesses to pick the best material for their specific needs without limitations.
4. Reduced Waste
Low-volume CNC machining is inherently sustainable. Since it is tailored for smaller production runs, there is less material wastage than traditional high-volume methods. This not only reduces costs but also aligns with eco-friendly manufacturing practices.
When to Use Low-volume CNC Machining?
How does a CNC machine work? After knowing it, let's learn when to use it. Low-volume CNC machining is an agile manufacturing strategy with a range of applications. Businesses looking to optimize their production processes must understand when to use it.
Conditions for Choosing Low-volume CNC Machining
Market Testing
Knowing how the market will respond is essential when introducing a new product. Low-volume CNC machining is perfect for this phase because it allows for small-batch production.
By producing small batches, businesses can gauge market demand and receive valuable feedback. This insight allows for adjustments to the product design, materials, or manufacturing processes before committing to large-scale production. It is a cost-effective way to minimize risks associated with untested products.
Quality Control
Rapid CNC machining offers a highly precise and repeatable manufacturing process. This consistency guarantees that each part or component meets stringent quality standards. Businesses can closely monitor quality, make necessary adjustments, and uphold quality control without the complexities that come with large-scale production.
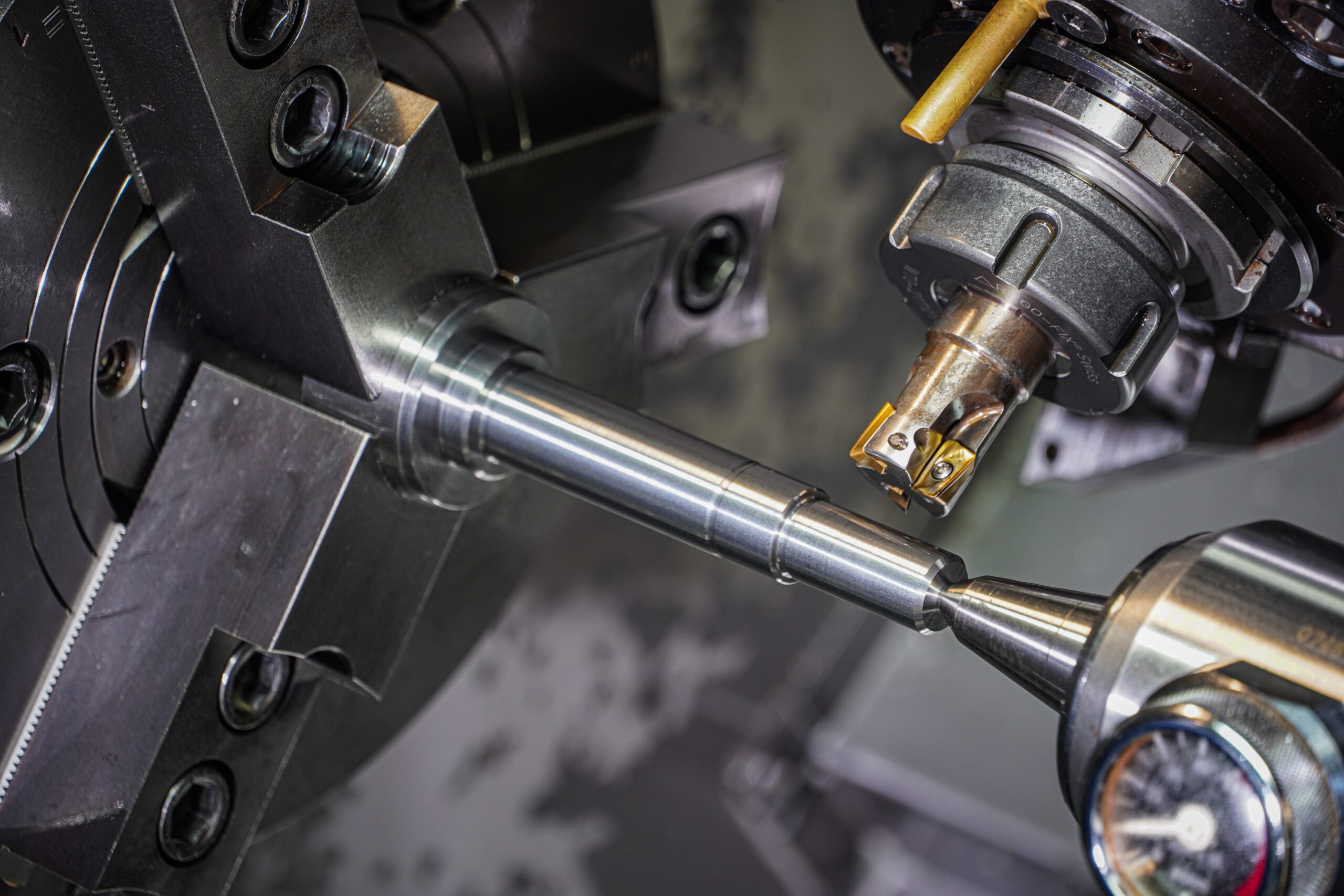
Production of Complex Geometries
Some product designs feature intricate and challenging shapes that are challenging to produce using traditional manufacturing methods. Precision-crafted complex geometries are a specialty of low-volume CNC machining. Rapid CNC machining makes sure that even the most complex designs are produced accurately and consistently, whether it be prototypes, custom parts, or components with intricate contours.
When to Use Different Types of Low-volume CNC Machining Operations
Small CNC machines can perform various operations which are designed to execute specific manufacturing needs:
- CNC Drilling
CNC drilling is the go-to operation for creating precise holes in parts. It is used for tasks like creating mounting holes, fastener holes, or fluid passageways. The accuracy and repeatability of this rapid CNC machining ensure consistent results, making it essential in various industries. - CNC Milling
CNC milling is a versatile operation that involves cutting and shaping materials. It is particularly useful for producing intricate 2D and 3D shapes. Businesses often turn to this valuable equipment for prototyping and creating complex parts that demand precision and accuracy. - CNC Turning
CNC turning specializes in crafting cylindrical or rotational parts. This operation is commonly used for producing shafts, rods, and other rotating components. Its precision and efficiency make it a valuable choice in many manufacturing processes. - CNC Grinding
CNC grinding is the preferred operation when extremely precise surface finishing is required. It is used to produce incredibly fine surface finishes and tight tolerances. It is used in industries such as aerospace and medical device manufacturing because of their stringent requirements.
HordRT for Rapid CNC Machining Services
HordRT stands out as your trusted partner for rapid CNC machining services. We specialize in both plastic and metal CNC machining, delivering rapid prototypes in as little as one day. With a monthly production capacity exceeding 10,000 CNC parts, we ensure top-notch quality with tolerance accuracy ranging from +/- 0.001 to 0.005.
Get an instant quote and experience excellence with HordRT’s CNC machining services today!