Contents
Die casting is a versatile and widely used manufacturing process that involves injecting molten metal into a cavity under high pressure. This is essential in producing complex and precise metal parts, which are crucial in various industries, including automotive, electronics, aerospace, and consumer goods, etc. The efficiency and accuracy of die casting make it a preferred choice for mass production of metal components.
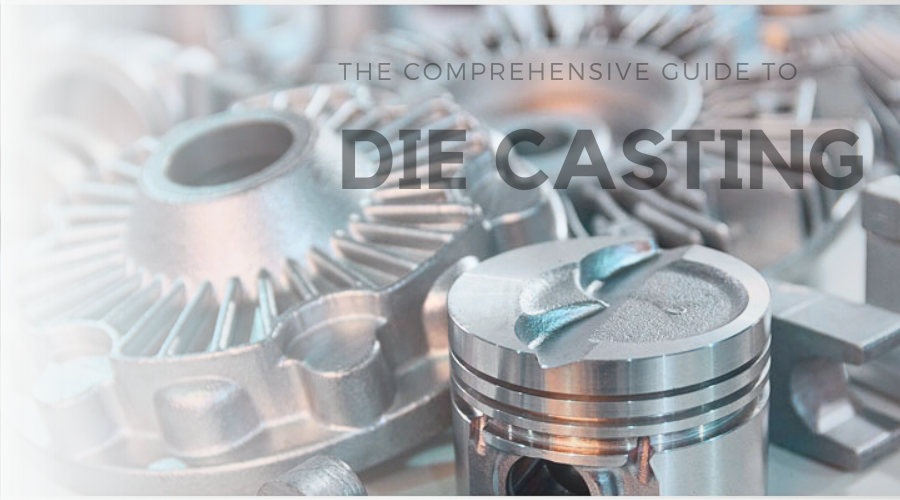
Die Casting Process
The die casting process consists of several critical steps, each ensuring the creation of high-quality metal parts:
1. Mold Preparation: The die, made from hardened tool steel, is designed and prepared. It typically consists of two halves: the fixed half (cover die) and the moving half (ejector die).
2. Melting and Injection: The chosen metal is melted in a furnace. In the hot chamber process, the molten metal is directly injected into the mold. In the cold chamber process, the molten metal is ladled into the injection system.
3. Cooling: Once the metal is injected, it quickly cools and solidifies, taking the shape of the mold cavity.
4. Ejection: After solidification the mold opens, and ejector pins push the casting out of the die.
5. Finishing: The casting is cleaned, trimmed, and finished to remove any excess material or imperfections.
Materials Used in Die Casting
Various metals can be used in die casting, and each offers unique properties:
- Aluminum: Know for its lightweight, corrosion resistance, and high strength-to-weight ratio, aluminum is commonly used in automotive and aerospace applications.
- Zinc: Zinc offers high ductility, and impact strength, and is easily plated, making it suitable for intricate designs and high-volume production.
- Magnesium: The lightest structural metal, magnesium provides excellent strength and is used in applications where weight reduction is critial.
- Copper: With excellent electrical conductivity and corrosion resistance, copper is ideal for electrical components.
Types of Die Casting
There are two primary types of die casting processes, each suited to different applications and materials:
- Hot Chamber Die Casting: In this method, the metal is melted in a chamber connected to the die cavity. It is faster and more efficient, suitable for metals with low melting points such as zinc and magnesium. However, it is not suitable for high-melting-point metals like aluminum.
- Cold Chamber Die Casting: This process involves dadling molten metal into the injection system. It is used for metals with higher melting points, such as aluminum and copper. Although slower than the hot chamber process, it allows for the casting of larger and more complex parts.
Available Die Casting Finishes
Die casting is not only about creating precise and complex metal parts but also about achieving the desired surface finish. Various finishing techniques can enhance the appearance, functionality, and durability of die-cast parts. Here are some commonly used die casting finishes:
- As-Cast Finish
- Description: The part is used as it comes out of the die without any additional finishing.
- Applications: suitable for internal components or parts where surface appearance is not critical.
- Advantages: Cost-effective and quick.
- Polishing
- Description: The surface is mechanically polished to achieve a smooth and shiny finish.
- Applications: Automotive parts, decorative items, and consumer goods.
- Advantages: Enhances aesthetic appeal and provides a reflective surface.
- Shot Blasting / Sand Blasting
- Description: The part is blasted with abrasive materials to remove surface imperfections and create a uniform texture.
- Application: Preparing surfaces for painting or coating, and enhancing the overall appearance.
- Advantages: Removes residues and improves adhesion for subsequent coatings.
- Power Coating
- Description: A dry power is electrostatically applied to the part and then cured under heat to form a hard finish.
- Applications: Outdoor equipment, automotive parts, and appliances.
- Advantages: Provides a durable, corrosion-resistant finish with a wide rang of color options.
- Painting
- Description: Liquid paint is applied to the part using various techniques such as spraying or dipping.
- Applications: Consumer electronics, automotive components, and decorative items.
- Advantages: Offers a variety of colors and finishes, including glossy, matte and textured.
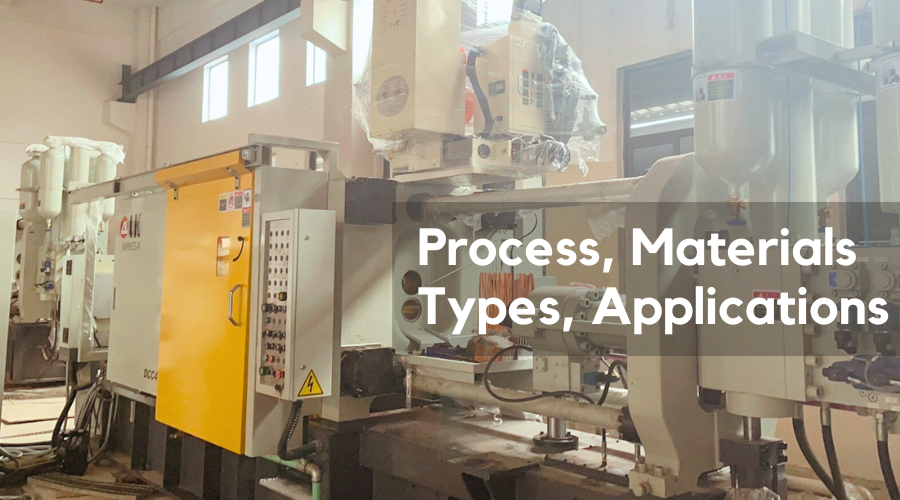
- Anodizing
- Description: An electrolytic process that enhances the natural oxide layer on the surface of aluminum parts.
- Applications: Aerospace components, electronics, and consumer goods.
- Advantages: Increase corrosion resistance, wear resistance, and can add vibrant colors.
- Electroplating
- Description: A metal coating is deposited on the surface of the part using an electric current.
- Applications: Automotive parts, electrical connectors, and decorative items.
- Advantages: Provides a hard, wear-resistant surface with improved conductivity and corrosion resistance.
- Chromate Conversion Coating
- Description: A chemical process that applies a protective chromate layer on the surface of the part.
- Applications: Military and aerospace components, electronics, and fasteners.
- Advantages: Enhances corrosion resistance and provides a good base for painting.
- Passivation
- Description: A chemical treatment that removes free iron from the surface and enhances the natural protective oxide layer on stainless steel.
- Applications: Medical devices, food processing equipment, and marine applications.
- Advantages: Increases corrosion resistance without changing the appearance of the part.
- Electrophoretic Coating (E-coating)
- Description: A process where the part is submerged in a paint bath and an electric current is used to deposit the pain onto the surface.
- Applications: Automotive components, appliances, and metal furniture.
- Advantages: Provides uniform coverage, even on complex geometries, and excellent corrosion resistance.
Applications of Die Casting
Die casting is integral to various industries due to its ability to produce precise and complex parts efficiently:
- Automotive Industry: Engine blocks, transmission housings, and other critical components.
- Electronics: Housings, connectors, and heat sinks.
- Aerospace: Lightweight structural components and avionics parts.
- Consumer Goods: Appliance parts, hardware, and toys.
- Industrial Applications: Machinery parts and tools.
Advantages and Disadvantages of Die Casting
Die casting offers several benefits:
- High Production Rate: Efficient and cost-effective for large-scale production.
- Dimensional Accuracy: Produces parts with precise dimensions and smooth finishes.
- Surface Finish: High-quality surface finish reduces the need for additional machining.
However, it also has come limitations:
- High Initial Cost:Significant investment in tooling and equipment.
- Material Restrictions: Limited to metals with specific melting points and properties.
- Part Size Limitations: Suitable mainly for smaller to medium-sized parts.
Conclusion
Die casting remains a crucial manufacturing process for producing high-quality metal parts efficiently. Its applications across various industries highlight its importance in modern manufacturing. As technology advances, innovations in die casting are expected to further enhance its capabilities, making it even more versatile and valuable in the future.
For superior die casting solutions, choose HordRT Die Casting Service. We excel in providing high-quality, precise metal components customized to meet your exact requirements. Our advanced technology and skilled team guarantee exceptional results for every project, whether it's in the automotive, electronics, aerospace, or consumer goods sectors. Rely on HordRT for your die casting needs and experience unparalleled quality and performance. Contact us now!