Silk screen printing, also known as screen printing or serigraphy, is a versatile and cost-effective method for adding grapgics, logos, labels, and text to a wide range of surfaces, including injection molded parts. This printing technique has been around for centuries and has evolved into a highly efficient and customizable process that is widely used in industries such as automotive, electronics, medical device, consumer products, and more. In this article, we will explore the benefits and applications of silk screen printing for injection molded parts.
The Basics of Silk Screen Printing
Silk screen printing involves transferring ink through a mesh screen onto the surface of the substrate, leaving a desired design or pattern. The mesh screen is tightly stretched over a frame, and a stencil or template is placed on top. The stencil contains openings that correspond to the areas where ink should pass through, creating the desired image or text. The ink is applied to the screen, and a squeegee is used to push the ink through the stencil and onto the substrate. The result is a precise and highly detailed print on the surface.
Benefits of Silk Screen Printing for Injection Molded Parts
- Durability: One of the primary advantages of silk screen printing is its durability. The ink adheres well to the surface of injection molded parts, making it resistant to wear, abrasion, and environmental factors. This is crucial for parts that may be subjected to various stressors in their intended applications.
- High Resolution and Detail: Silk screen printing can achieve high resolution and fine detail in prints. This makes it ideal for adding intricate designs, logos, and text to injection molded parts, ensuring that the branding or information is clear and visually appealing.
- Color Customization: Silk screen printing allows for precise color matching, enabling companies to reproduce their branding and design elements accurately. This is essential for maintaining brand consistency and aesthetics across a product line.
- Versatility: This printing method is versatile and can be applied to a wide range of materials, including plastics, metals, glass, and more. It is particularly well-suited for injection molded plastic parts, as it can adapt to various shapes and sizes.
- Cost-Effective: Silk screen printing is a cost-effective solution, especially for large production runs. The process is relatively quick and efficient, making it a practical choice for mass-producing injection molded parts.
- Adhesion and Compatibility: The inks used in silk screen printing are formulated to adhere well to different materials, including various types of plastics used in injection molding. This ensures that the prints remain intact and vibrant throughout the product’s lifespan.
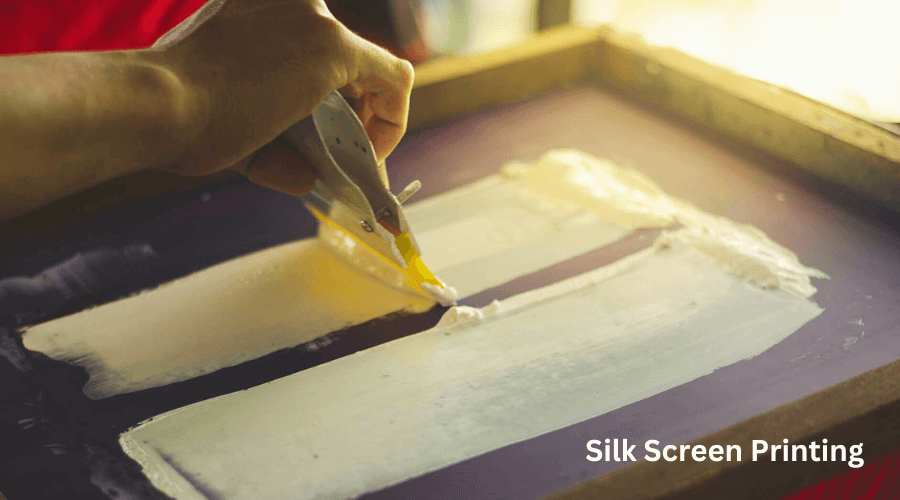
The process of Silk Screen Printing of Injection Molded Parts
- Artwork preparation: The process begins with the creation or preparation of the artwork of design that will be printed onto the injection-molded part. This design is typically produced using graphics design software and should be in a format suitable for screen printing. It is essential to create a design with clear, defined lines and areas of color.
- Screen Preparation: A mesh screen, often made of polyester or stainless steel, is tightly stretched over a frame to create a smooth and taut surface. The choice of mesh count (the number of threads per inch) on the screen determines the level of detail that can be achieved in the print. A higher mesh count allows for finer details but may require more precise printing techniques.
- Stencil Creation: A stencil, also known as a screen or template, is created based on the design. There are different methods for producing stencils, but one common approach involves uing light-sensitive emulsion. The stencil includes areas that permit ink to pass through (corresponding to the design) and areas that block the ink. The stencil is attached to the screen.
- Registration: Proper registration is essential for accurate printing. The screen is positioned above the injection-molded part, ensuring that the stencil and the part are correctly aligned. This step ensures that the print is precise and matches the design.
- Ink selection: Screen printing ink is chosen based on the material of the injection-molded part and the desired colors. Specialized inks are available for various substrates, including plastics, metals, and glass. The ink is mixed to achieve the desired color and viscosity.
- Printing: Ink is applied to the screen’s frame, covering the stencil. A squeegee is then used to press the ink through the openings in the stencil and onto the surface of the injection-molded part. The squeegee is moved evenly and consistently across the screen to ensure an even and uniform print.
- Curing or Drying: To achieve proper adhesion and durability, the ink on the injection-molded part must be cured or dried. The method of curing depends on the type of ink used and can involve air drying, heat curing, or ultraviolet(UV) curing.
- Quality Control: Printed parts undergo a thorough quality control inspection to ensure that the print is of high quality with no defects, inconsistencies, or imperfections. Any issues are addressed and necessary adjustments are made.
- Cleaning and Reclamation: After printing, the screen and equipment are cleaned to remove excess ink and emulsion, making them ready for future use. Any remaining ink is properly disposed of, and the screen are prepared for the next printing job.
- Packaging and Shipping: Once the printed injection-molded parts have passed quality control, they are packaged and prepared for shipping or further assembly, depending on the specific product’s requirements.
Wrapping Up
In conclusion, silk screen printing is a valuable and versatile technique for enhancing the appearance, functionality, and branding of injection molded parts. Its durability, precision, and cost-effectiveness make it a top choice for industries spanning automotive, electronics, medical devices, and more. When choosing a printing method for your injection molded parts, silk screen printing should be considered for its ability to provide enduring and aesthetically pleasing results.