
Johnny Xiong
Rapid Tooling Expert
Contents
Injection molding is one of the most widely used manufacturing processes for producing plastic parts with high precision and efficiency. However, like all industrial processes, it is susceptible to defects. One of the most common and frustrating defects is the short shot, which occurs when the mold cavity is not completely filled during injection. This article provides a comprehensive look at short shot defects in injection molding, exploring their causes, how to detect them, and effective strategies for prevention.
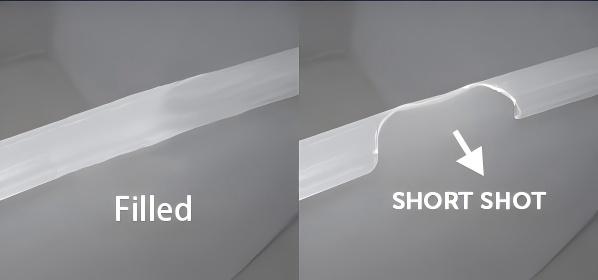
What is a Short Shot in Injection Molding?
A short shot refers to an incomplete filling of the mold cavity, resulting in a part that is missing material or has incomplete geometry. The plastic does not reach all areas of the mold, leaving voids or unformed sections. This defect compromises the functionality, strength, and aesthetic of the final product, making it unacceptable for most industrial or consumer applications.
Visual Characteristics of a Short Shot
A short shot defect can usually be identified by:
Unfilled or missing sections of the molded part
Rough or irregular edges at the end of the flow path
Reduced part size or dimension in the affected region
Surface finish inconsistencies
Common Causes of Short Shot Defects
Short shots can be attributed to several root causes. Understanding these is key to effectively solving the issue.
1. Insufficient Injection Pressure or Speed
If the injection pressure is too low or the speed is too slow, the molten plastic may not have enough force to reach all areas of the mold cavity before solidifying.
Solution: Increase injection pressure and speed settings to ensure complete mold filling.
2. Inadequate Melt Temperature
Plastic that is too cool becomes viscous and does not flow well. This can prevent it from completely filling the mold.
Solution: Adjust the barrel temperature settings to match the material’s recommended processing range.
3. Poor Mold Design
Design-related issues such as long, thin flow paths, sharp corners, or improperly placed gates can restrict the flow of molten plastic, leading to short shots.
Solution: Optimize mold design with proper gate placement, flow channels, and venting. Use mold flow simulation software to predict and address potential flow issues.
4. Improper Venting
Air trapped in the mold cavity can prevent the plastic from filling certain areas, resulting in incomplete parts.
Solution: Improve mold venting systems to allow air to escape easily. Add or enlarge vents in critical areas.
5. Material-Related Issues
Some materials have poor flow characteristics or require specific processing parameters. Regrind content or contamination can also impact flow behavior.
Solution: Choose materials with better flow properties for complex molds. Avoid using excessive regrind or contaminated materials.
6. Clogged or Worn Gates, Runners, or Nozzles
Blockages or wear in the injection system can restrict plastic flow, causing incomplete fills.
Solution: Regularly inspect and maintain the injection unit and mold components. Clean or replace damaged parts.
7. Inadequate Shot Size
The amount of plastic injected (shot size) may be less than what is required to fill the cavity.
Solution: Increase shot size in the machine settings to ensure there is enough material to fill the mold.
How to Detect Short Shots
Early detection is crucial to avoid high scrap rates and wasted production time. Detection methods include:
1. Visual Inspection
Operators can check parts immediately after molding for obvious signs of incomplete fill.
2. Weight Measurement
Short shots typically result in parts that are lighter than normal. Automated scales can detect underweight parts.
3. Camera and Vision Systems
Advanced production lines use machine vision to detect defects in real-time.
4. Mold Cavity Pressure Monitoring
Sensors in the mold monitor pressure and can detect irregular filling behavior.
Preventing Short Shot Defects: Best Practices
Avoiding short shots requires a combination of correct design, proper machine settings, material control, and regular maintenance.
1. Optimize Injection Parameters
Injection speed and pressure: Increase as necessary to ensure complete mold filling.
Melt temperature: Maintain within the recommended range for the plastic resin.
Back pressure: Adjust to improve melt homogeneity.
2. Improve Mold Design
Ensure uniform wall thickness
Use flow leaders and flow channels to assist filling
Optimize gate type, location, and size
Add adequate venting
3. Select the Right Material
Choose materials with appropriate melt flow index (MFI)
Avoid degraded or high-regrind content resins
Store materials properly to prevent moisture contamination
4. Machine Maintenance
Clean nozzles, runners, and gates regularly
Check for wear or damage in screws and barrels
Verify clamp force to avoid flash or incomplete sealing
5. Use Simulation Tools
Mold flow analysis can help predict short shot problems before the mold is built. These simulations allow designers to test gate placement, part orientation, and material behavior virtually.
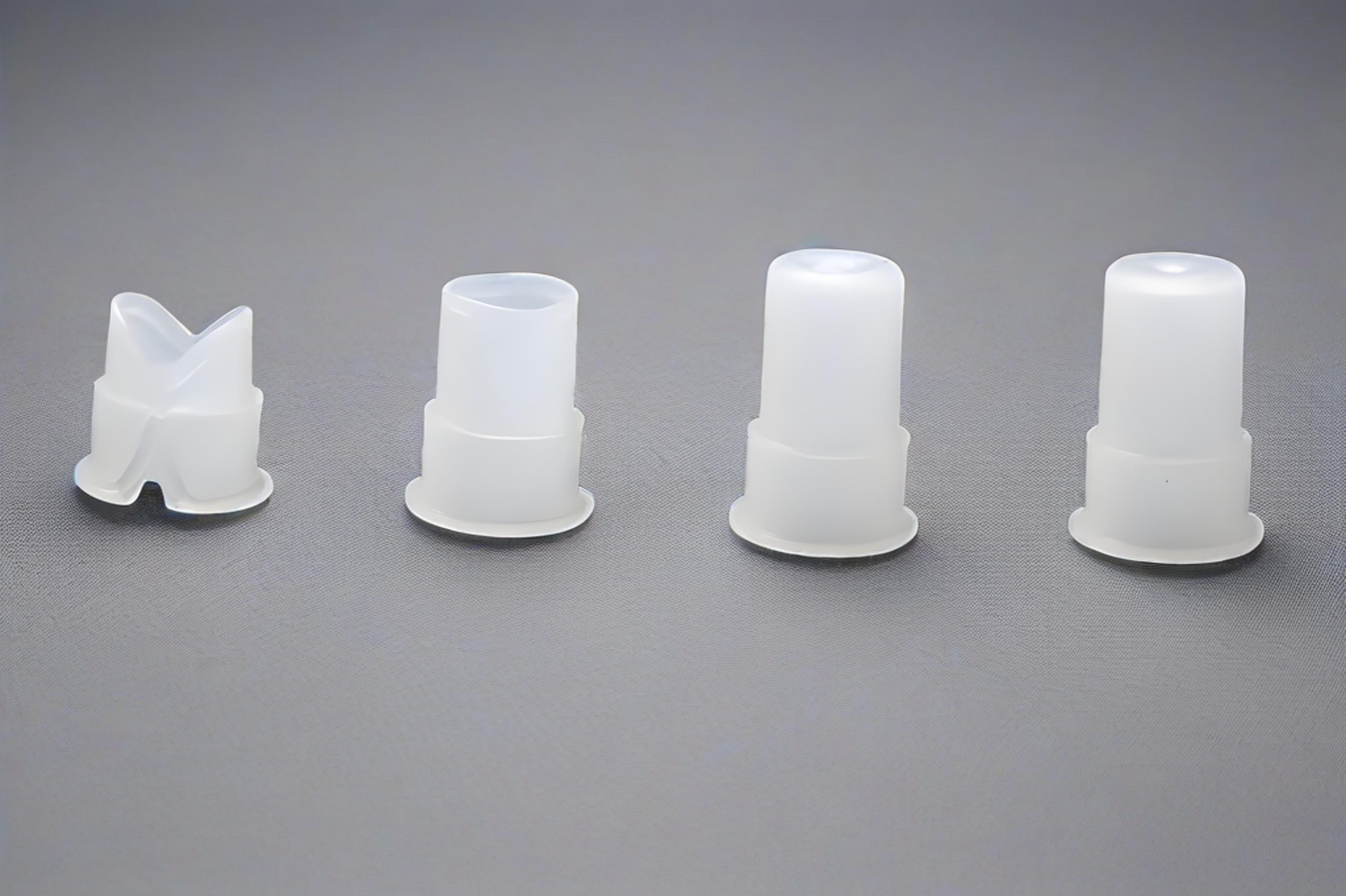
Case Study: Short Shot in a Multi-Cavity Mold
Scenario: A customer experienced inconsistent filling in a 4-cavity mold for a small consumer electronics housing.
Findings:
One cavity consistently produced short shots.
The gate for that cavity was slightly smaller due to a manufacturing error.
The mold lacked sufficient venting in that cavity.
Solution:
The gate was re-machined to match the others.
Additional vents were added to improve air escape.
Injection pressure and speed were fine-tuned.
Result: The short shot issue was resolved, and part quality stabilized across all cavities.
Impact of Short Shots on Product Quality
Short shots directly affect product performance and aesthetics, which can result in:
Poor structural integrity
Cosmetic defects
Assembly issues
Customer complaints and product recalls
Increased production costs and downtime
Conclusion
Short shot defects in injection molding can lead to severe consequences in terms of product quality, customer satisfaction, and manufacturing efficiency. By understanding the underlying causes, utilizing detection tools, and implementing proven prevention strategies, manufacturers can significantly reduce or eliminate short shots.
At HordRT, we specialize in high-precision injection molding services with a strong focus on quality assurance and defect control. Our engineering team uses advanced mold flow simulation, robust quality checks, and optimized process parameters to deliver reliable, high-performance parts — every time.
Need help eliminating short shots in your injection molding project?
Contact HordRT today and let our experts assist with mold optimization, troubleshooting, and manufacturing solutions.