In the intricate realm of product manufacturing, achieving optimal quality and efficiency is a constant pursuit. One technology that has significantly contributed to this endeavor is Mold Flow Analysis. This innovative process has revolutionized the way products are designed, developed, and produced, leading to improved final outcomes and reduced production costs.
In this article, we delve into the world of Mold Flow Analysis, exploring its fundamentals, functionality, and the myriad benefits it offers to manufacturers.

What is Mold Flow Analysis
Mold Flow Analysis, often referred to as MFA, is a sophisticated simulation technique used in the manufacturing industry to predict the behavior of molten plastic within a mold during the injection process. Injection molding is a common manufacturing method for producing plastic parts, where molten plastic is injected into a mold cavity, allowed to cool and solidify, and then ejected as a finished product. Mold Flow Analysis provides manufacturers with invaluable insights into the flow of plastic, temperature distribution, pressure points, and potential defects within the mold, all before the actual manufacturing process takes place.
How Does Mold Flow Analysis Work?
Mold Flow Analysis involves the utilization of advanced computer software to simulate the injection molding process. The process can be broken down into several key steps:
- Geometry Import: The part's digital model the manufactured is imported into the Mold Flow Analysis software. This model includes all the intricate details of the part’s design, such as dimensions, shapes, and features.
- Material Properties: The software requires information about the material to be used in the injection molding process. Properties like melt flow rate, viscosity, thermal conductivity, and shrinkage are inputted to ensure accurate simulations.
- Mesh Generation: The software divides the digital model into a finite number of more minor elements, known as mesh elements. This mesh enables the software to simulate the behavior of the material at different points within the mold.
- Simulation: With the geometry, material properties, and mesh in place, the software simulates the injection molding process. It predicts how the molten plastic will flow, how it will cool and solidify, and how various factors such as pressure, temperature, and flow rate will influence the final part.
- Analysis: The simulation results are analyzed to identify potential issues, such as air traps, weld lines, shrinkage, warpage, and other defects that might arise during the actual manufacturing process.
- Optimization: manufacturers can make informed design and process adjustments based on the simulation results. This might involve modifying the mold design, adjusting material properties, or altering the injection molding parameters.
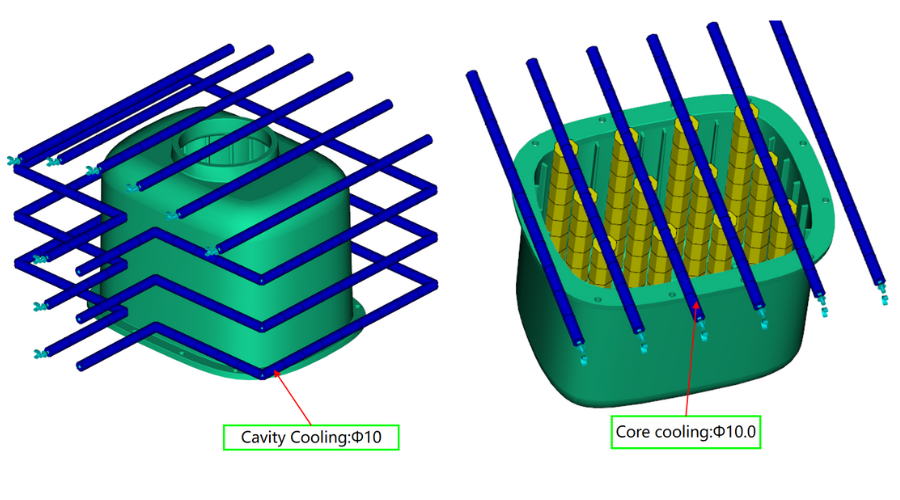
Benefits That Mold Flow Analysis Brings
- Improved Design:Mold Flow Analysis enables designers to identify potential flaws and challenges in the initial product design, leading to optimized designs that are easier to manufacture and exhibit fewer defects.
- Cost Saving: By identifying and rectifying issues in the virtual environment, manufacturers can avoid costly and time-consuming trial-and-error processes during actual production.
- Faster Time-to-Market: Mold Flow Analysis accelerates the design iteration process, enabling faster development and reduced time-to-market for new products.
- Enhanced Quality: The ability to predict and prevent defects results in higher-quality end products that meet or exceed customer expectations.
- Process Optimization: Manufacturers can fine-tune the injection molding process parameters to achieve optimal results, reducing material waste and energy consumption.
- Risk Mitigation: By simulating various scenarios, manufacturers can anticipate potential problems and make informed decisions to mitigate risks associated with the injection molding process.
Wrapping up
Mold Flow Analysis has emerged as a game-changer in the field of product manufacturing. It empowers manufacturers to anticipate challenges, optimize designs, enhance product quality, and streamline the production process. By harnessing the power of advanced simulations, companies can achieve their goals of producing high-quality products while maintaining cost-efficiency and competitive advantage in today’s dynamic market landscape.
At HordRT, our services encompass mold flow analysis accompanied by expert recommendations to enhance your design. Feel free to engage with our support team for valuable manufacturing insights. If you possess a CAD file, take advantage of the option to upload it and receive an immediate quote for your envisioned design.