Injection molding is a widely used manufacturing process for producing plastic parts and products. It involves injecting molten material into a mold cavity, allowing it to cool and solidify before ejecting the final product. One important decision manufacturers must make when using injection molding is whether to opt for a single-cavity or multi-cavity approach. Each method has its advantages and considerations, and selecting the right approach can significantly impact production efficiency, cost-effectiveness, and overall project success. In this article, we will explore the differences between single-cavity and multi-cavity injection molding and provide insights to help you make an informed decision.

Single-Cavity Injection Molding
Single-cavity injection molding refers to the process of creating one part per mold cycle. This approach involves using a mold with a single cavity impression, where molten material is injected to form a single product. Here are some key points to consider when using single-cavity injection molding:
Flexibility and Simplicity: Single-cavity molds offer great flexibility, especially for low-volume production or when manufacturing complex parts. They allow for easy modifications and adjustments to the mold design, making it suitable for prototyping and small-scale production runs
Quality Control: Single-cavity molds enable manufacturers to have better control over the production process, as they can closely monitor and optimize each individual mold cycle. This can result in improved quality and consistency of the final products.
Longer Cycle Times: Since only one part is produced per cycle, single-cavity injection molding tends to have longer cycle times compared to multi-cavity molding. This can limit production throughput and increase manufacturing lead times, making it less suitable for high-volume production.
Higher Cost per Part: Single-cavity molding generally incurs higher tooling costs since each cavity requires a separate mold. Consequently, the cost per part is typically higher for single-cavity molds, making it less economical for large-scale production.
Multi-Cavity Injection Molding
Multi-cavity injection molding involves creating multiple parts simultaneously within a single mold cycle. By incorporating multiple cavities within a single mold, manufacturers can produce more parts per cycle, increasing overall production efficiency. Here are some key points to consider when using multi-cavity injection molding:
Increased Production Efficiency: The primary advantage of multi-cavity injection molding is the ability to produce a higher number of parts in a shorter time. By utilizing multiple cavities within a single mold, manufacturers can significantly increase production output, making it ideal for high-volume manufacturing.
Reduced Cost per Part: With multi-cavity molding, the tooling costs are distributed across multiple cavities, resulting in a lower cost per part. This cost advantage makes it a preferred choice for large-scale production, where economies of scale play a crucial role.
Complex Design Considerations: The design and layout of the part can influence the feasibility of multi-cavity molding. Certain parts may have challenging geometries or require specific gating and cooling strategies to ensure uniform quality across all cavities. It is important to assess the part design and consult with mold design experts to determine the suitability of multi-cavity molding.
Maintenance and Repairs: Multi-cavity molds can be more complex and require more maintenance compared to single-cavity molds. When one cavity requires repair or maintenance, it may affect the entire production cycle. However, proper mold maintenance and monitoring can mitigate these challenges.
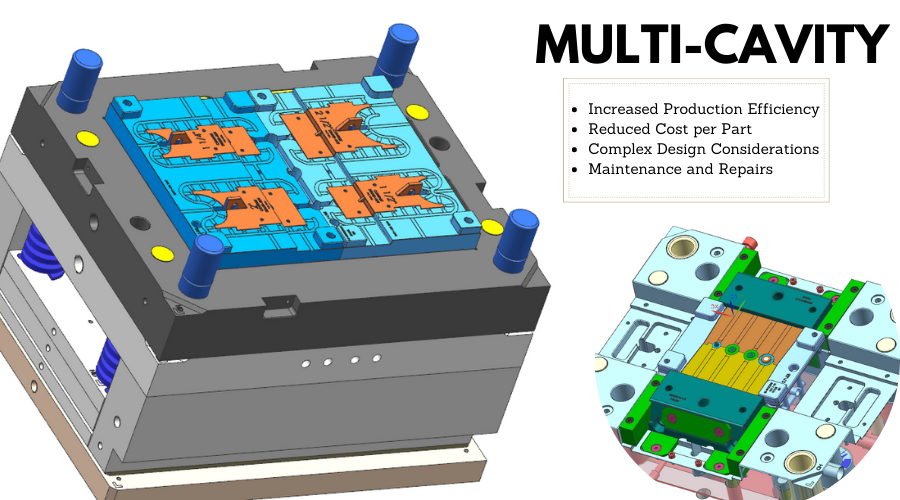
How to Choosing the Right Approach
Deciding between single-cavity and multi-cavity injection molding depends on various factors specific to your project requirements. Here are some considerations to help you make the right choice:
Production Volume: Evaluate your production volume needs. Single-cavity molding is suitable for low-volume production or prototyping, while multi-cavity molding is ideal for high-volume production.
Time-to-Market: Consider the speed you need to bring your product to market. Single-cavity molding offers flexibility and quicker iterations, while multi-cavity molding can expedite production but may require more upfront planning and validation.
Cost Considerations: Assess your budget and cost targets. Single-cavity molding generally has higher tooling costs and higher costs per part, while multi-cavity molding can offer cost advantages for large-scale production.
Part Complexity: Evaluate the complexity of your part design. Some parts may be better suited for single-cavity molding due to their intricate features or specific material requirements.
Quality Requirements: Consider the desired quality standards for your parts. Single-cavity molding allows for better control and monitoring of each part, which can be beneficial for maintaining high quality. However, advancements in multi-cavity molding techniques have also made it possible to achieve consistent quality across multiple cavities.
Tooling and Equipment: Assess your available tooling capabilities and equipment. Single-cavity molds are generally less complex and require simpler equipment setups. Multi-cavity molds may require more advanced equipment and skilled operators to ensure proper functioning and maintenance.
Scalability and Future Needs: Think about your long-term goals and potential scalability. If you anticipate an increase in production volume over time, multi-cavity molding can accommodate higher output more efficiently. Single-cavity molding may require redesigning and remanufacturing molds as your production needs expand.
Project Timeline: Evaluate your project timeline and turnaround requirements. Single-cavity molding typically allows for faster modifications and adjustments, making it more suitable for projects with shorter development cycles. Multi-cavity molding may involve more planning and lead time for mold manufacturing and validation.
Risk Assessment: Consider the potential risks and challenges associated with each approach. Single-cavity molding offers more flexibility and control but may have longer cycle times and higher costs. Multi-cavity molding provides higher production efficiency but requires careful design considerations and maintenance.

In conclusion, the decision between single-cavity and multi-cavity injection molding depends on a comprehensive evaluation of project requirements. Factors such as quality requirements, tooling and equipment, scalability, project timeline, and risk assessment are crucial considerations. Our company is dedicated to injection molding and emphasizes meeting the specific needs of our clients.
As an injection molding specialist, HordRT focuses on understanding our client's requirements and providing comprehensive solutions. Whether it's single-cavity or multi-cavity molding, we offer tailored advice and services based on project requirements and objectives. With advanced equipment and expertise, we can select the most suitable injection molding approach based on part complexity and quality requirements, ensuring the optimal balance of product quality, production efficiency, and cost-effectiveness.