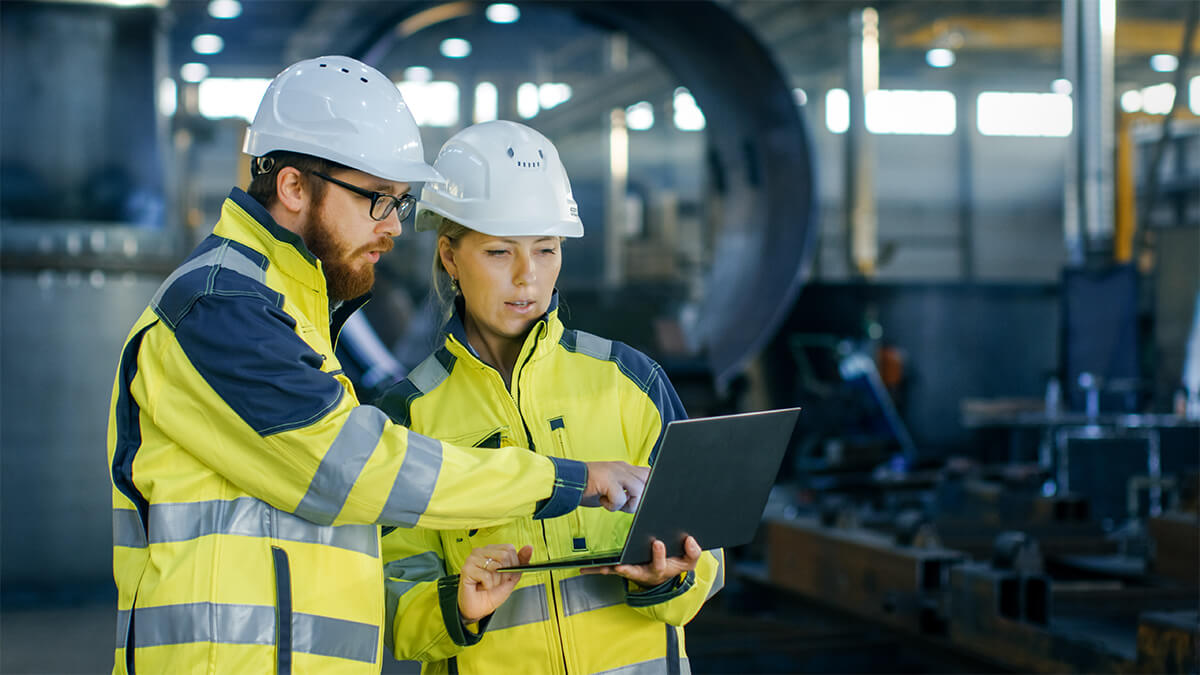
Choosing the right manufacturing process has a significant impact on the quality,aesthetic and cost of parts. Therefore, once decide to produce a part, the first consideration is to select a right manufacturing process for the parts. Here are some of the critical factors that should be considered while selecting the right manufacturing technology for your product.
The Tooling and Part Cost
There are two kinds of costs in the manufacturing process: Tooling Cost and Part Cost.
Tooling cost is the cost of creating the mold, jig or other one time setup cost associated with starting production. The part cost is the cost incurred each time a part is manufactured. Cost always matters when choosing a manufacturing technology.
Depending on the part molding process, the price to create a quality tool can be extremely high. For example, creating a steel tool for injection molding processes may cost several hundreds of thousands of dollars. The larger and more complex the part is, the higher the cost of tooling will be. While a lower individual part production cost may help offset the cost of a highly expensive tool for parts that are produced in extremely large quantities, this isn’t the case for parts that have lower production volumes.
Tooling cost is the cost of creating the mold, jig or other one time setup cost associated with starting production. The part cost is the cost incurred each time a part is manufactured. Cost always matters when choosing a manufacturing technology.
Depending on the part molding process, the price to create a quality tool can be extremely high. For example, creating a steel tool for injection molding processes may cost several hundreds of thousands of dollars. The larger and more complex the part is, the higher the cost of tooling will be. While a lower individual part production cost may help offset the cost of a highly expensive tool for parts that are produced in extremely large quantities, this isn’t the case for parts that have lower production volumes.
PART GEOMETRY
When choosing the manufacturing process for the part, it is important to consider more nuanced attributes such as part geometry. According to the internal design of the part, the part needs to have advanced structural support or different wall thicknesses. Without extensive secondary operations, most part molding processes can only create parts with minimal differences in wall thickness. However, reaction injection molding provides the unique capability to produce parts with significant variations in wall thickness.
THE LEAD TIME
If parts need to be produced under strict time limits, the lead time of the part manufacturing process is also an important consideration. Many tooling processes can take 12 to 14 weeks, as they involve making tools and cutting metal, which is usually a time consultation. If need faster parts, some molding processes (such as thermoforming) have shorter lead times because no major molds are required. However, most processes with faster lead times produce parts with lower quality, require more secondary operations, and may not be repeatable. Therefore, you need to consider that quality or production time is a higher priority for the application.
PRODUCTION VOLUME
A project’s expected production volume represents one major determinant of which molding process will be utilized. If you plan on producing parts in large quantities (10,000+ annually), you may want to prioritize a molding process with lower individual part production costs even if entails more expensive tooling costs initially. For parts with higher production volumes, the higher cost of tooling is often offset by the lower cost of producing individual parts.
If you plan on creating parts in lower production volumes, however, processes with lower tooling costs are often advantageous because their cost-effective tooling options often offset other production expenses when items are manufactured in smaller quantities. RIM molding, for example, is ideal for parts with lower production volumes due to its far lower tooling cost than most other molding processes that create parts of similar quality.