Mold cores play a pivotal role in the world of manufacturing, particularly in processes such as injection molding and die casting. Understanding the intricacies of mold cores is essential for achieving high precision and quality in the production of complex parts and components. In this comprehensive guide, we will delve into the carious aspects of mold cores, including types, materials, design factors, and the manufacturing process.
What Is A Mold Core
A mold core is a crucial component in the mold-making process, serving as the internal cavity around which the material is injected or poured to create the final product. It is essentially the negative space within the mold, defining the shape and features of the finished part. Mold cores are integral to the production of intricate and precise components in industries ranging from automotive to consumer electronics.
Types of Mold Cores
- Fixed Cores: These cores remain stationary within the mold and do not move during the mold process. Fixed cores are commonly used for simpler part geometries where the removal of the core is not necessary.
- Movable Cores: Unlike fixed cores, movable cores can be retracted or rotated within the mold to facilitate the ejection of the finished part. This type is often employed in complex designs that require undercuts or internal features.
- Hydraulic Cores:These cores use hydraulic systems to move within the mold. Hydraulic cores are ideal for large-scale production where precision and speed are paramount.
- Rotating Cores:Employed in rotational molding, rotating cores enable the production of hollow parts. The mold rotates while the material is distributed, creating a uniform layer within the mold.
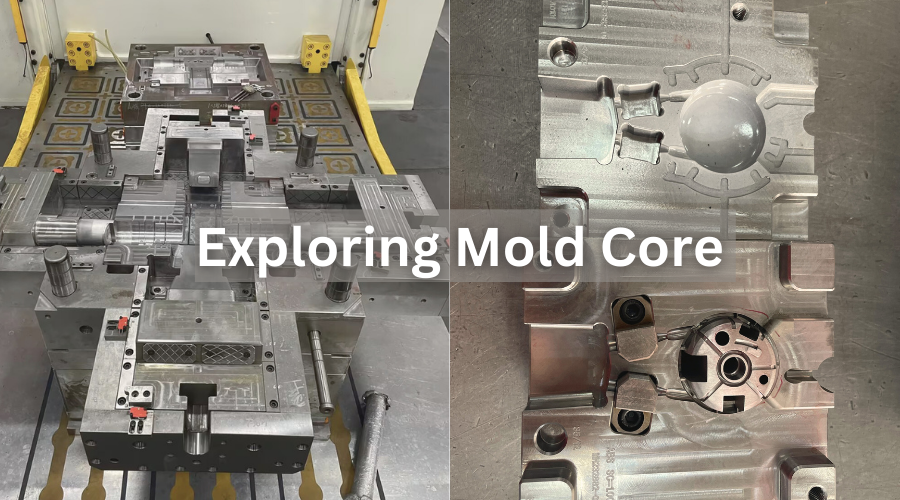
Materials Used in Making Mold Cores
Choosing the right material for mold cores is crucial for ensuring durability, thermal stability, and resistance to wear. Common materials include:
1. Tool Steel: Known for its high hardness and wear resistance, tool steel is a popular choice for mold cores, especially in high-volume production.
2. Aluminum: Aluminum cores are preferred for their lightweight properties and excellent thermal conductivity. They are suitable for rapid prototyping and low to medium production runs.
3. Beryllium Copper: This material offers high thermal conductivity, allowing for efficient heat dissipation during the molding process. It is particularly useful for applications requiring intricate details.
Key Considerations in Mold Core Design
1. Draft Angle: Incorporating draft angles in the mold core design facilitates the easy removal of the finished part, reducing the risk of damage and improving overall efficiency.
2. Undercuts: Molds with undercuts require movable cores to release the part successfully. Careful consideration of the part geometry is crucial to determine the optimal design for mold cores.
3. Cooling Channels: Efficient cooling is essential for maintaining consistent part quality. Designing mold cores with strategically placed cooling channels helps regulate temperature during the molding process.
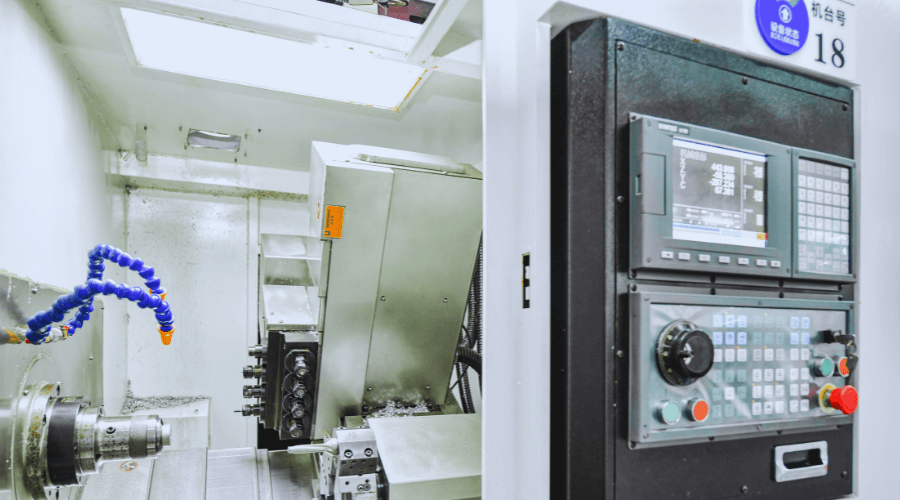
How to Make and Process the Mold Core
1. Designing the Mold Core: Utilize computer-aided design (CAD) software to create precise and detailed mold core designs.
2. Material Selection: Choose the appropriate material based on the production volume, part complexity, and desired properties. Work closely with material suppliers to ensure compatibility with the molding process.
3. Machining and Fabrication: Use advanced machining techniques such as CNC milling and EDM (electrical discharge machining) to accurately produce the mold core according to the design specification.
4. Heat Treatment: Apply heat treatment processes to enhance the hardness and durability of the mold core, ensuring it can withstand the stresses of repeated molding cycles.
5. Assembly and Testing: Assemble the mold core into the complete mold, incorporating any necessary hydraulic or mechanical components. Conduct thorough testing to validate the functionality and precision of the mold core.
Conclusion
In conclusion, mold cores are indispensable elements in the intricate world of manufacturing. Understanding the types, materials, design factors, and the manufacturing process is essential for achieving optimal results in part production. As technology advances and materials continue to evolve, the exploration of mold cores remains a dynamic field, driving innovation and efficiency in various industries. By staying informed and adopting best practices, manufacturers can harness the full potential of mold cores to create high-quality, precise, and intricate components for a wide range of applications.