Definition of die casting
Die casting is a manufacturing process used to produce metal parts with high precision and accuracy. It is a highly versatile process that is widely used in the automotive, aerospace, and consumer goods industries. In this article, we will explore the die-casting process, its advantages and limitations, and its applications.
Die casting is a process in which molten metal is injected into a mold cavity under high pressure. The mold is made of two halves, the fixed half called the "die" and the movable half called the "cover." The molten metal is injected into the mold through a sprue, and the pressure ensures that the metal fills the entire cavity, creating a high-quality, precise part.
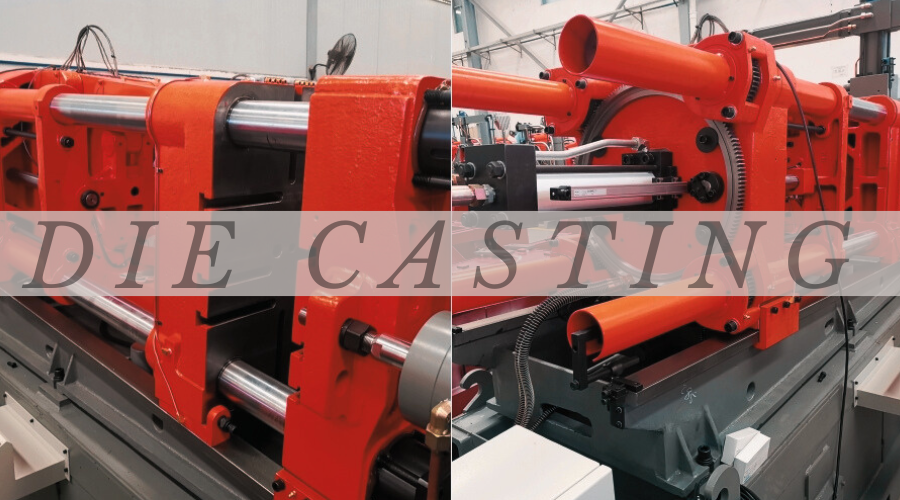
Types of Die Casting
There are two types of die casting: Hot chamber die casting and Cold chamber die casting.
Hot chamber die casting:the metal is melted in a furnace and then injected into the mold. The furnace is connected to the injection chamber, which is immersed in the molten metal. When the piston is pushed, the metal is forced into the mold.
Cold chamber die casting: In this process, the molten metal is kept in a separate chamber, which is not in direct contact with the injection system. The metal is ladled into the injection system and then injected into the mold under high pressure. This process is suitable for metals with a high melting point, such as aluminum, magnesium, and copper alloys.
Advantages of Die Casting
High Mechanical Properties
Die-cast products have excellent mechanical properties. When liquid metal solidifies under high pressure, the product appears fine, dense, and crystalline. Die castings are rigid, with high hardness and strength. In addition, they also improve durability and high conductivity.
High Dimensional Tolerance
Die casting produces parts with high durability and dimensional accuracy. Even when exposed to harsh conditions, parts will maintain their dimensional accuracy over time. Therefore, die casting is used to manufacture complex mechanical internal parts that require high standards of precision and accuracy.
Cost-Effective for Mass Production
Since the surface of die, castings is often smooth with excellent mechanical features, die-cast parts often require less machining. In some cases, no machining at all. As a result, there is less need to spend on secondary operations. The ability of die casting to reduce post-processing costs helps ensure its cost-effectiveness.
Smooth Surfaces
Die-casting parts have smooth and consistent crystalline surfaces. Die casting process alloys molten metal alloy to fill up the dies and create the exact shape. Therefore, provided the die is well-shaped and the process is in the right condition, the parts will be fine and smooth.
Because of making glossy parts, there is less need to proceed with additional post-processing operations, except for custom needs. What’s more, after die casting is done, products can be shipped off for delivery. This can reduce the total cycle production time.
Limitations of Die Casting
However, there are also some limitations to the die casting process. First, it is limited to the production of small to medium-sized parts, as larger parts would require larger and more expensive equipment. Second, it is not suitable for producing parts with very thin walls, as the molten metal may not fill the entire cavity. Third, it is not suitable for producing parts with very high strength requirements, as the process may introduce porosity and other defects.

Applications of Die Casting
Despite these limitations, the die-casting process is widely used in many industries. In the automotive industry, it is used to produce engine blocks, transmission cases, and other components. In the aerospace industry, it is used to produce turbine blades, compressor casings, and other parts. In the consumer goods industry, it is used to produce parts for appliances, toys, and electronics.
Conclusion
In a word, die casting is a highly versatile manufacturing process that allows for the production of high-precision and complex metal parts. While it has some limitations, its advantages make it a popular choice in many industries. As technology continues to advance, we can expect to see further improvements in the die casting process, making it an even more essential tool for modern manufacturing.