CNC milling is an integral part of modern manufacturing, offering precision and efficiency that are hard to match with traditional methods. It is a subtractive manufacturing process that uses computer-controlled milling machines to shape materials by removing excess material. It's widely used for creating complex parts with high precision and accuracy, from automotive components to aerospace equipment.
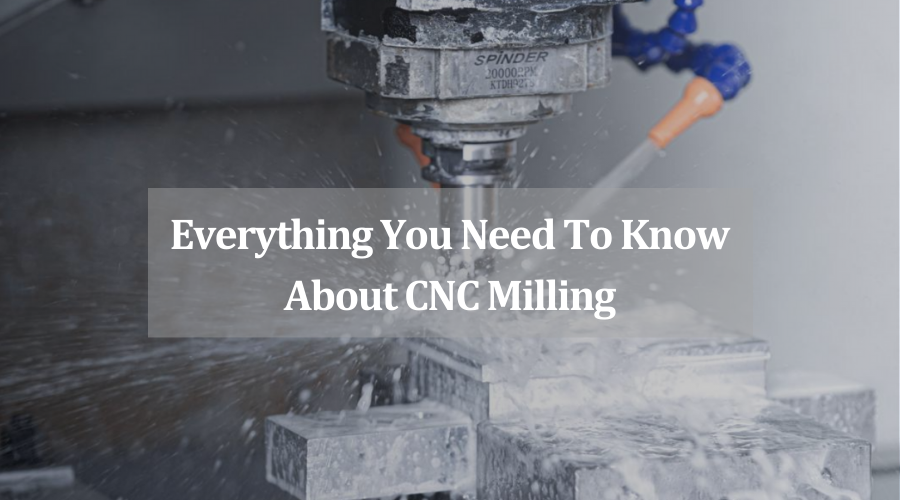
Understanding CNC Milling Machines
CNC milling machines are capable of producing parts with intricate details and exacting specifications. At the heart of this technology is a blend of mechanical components and computer control that work in harmony to shape materials with remarkable accuracy.
Operation of the CNC Milling Machine
The machine's operation begins with the creation of a 3D model of the desired part, which is then converted into G-code -- a series of instructions that dictate the machine's movements and actions. The G-code is uploaded to the control unit, which in turn actuates the machine's motors to position the spindle and workpiece accordingly.
The milling cutter, rotating at a specified speed, is brought into contact with the workpiece, removing material layer by layer. The precision of the machine ensures that each layer is cut to the exact dimensions specified in the program, resulting in a part that matches the design specifications.
The Coordinate System and Axes of Motion in CNC Milling
The coordinate system in CNC milling is akin to a roadmap for the machine, defining the exact path that the milling cutter will follow to create the part.
- Axes of Motion:
- X-Axis (Left-Right): Horizontal movement from left to right, controlled by the linear motion of the table or the spindle head.
- Y-Axis (Front-Back): Also horizontal, this axis moves the table or spindle head from the front to the back of the machine.
- Z-Axis (Up-Down): Vertical movement, allowing the spindle to approach or retract from the workpiece along the column.
- A, B, or C-Axis (Rotational): These rotational axes allow for the orientation of the workpiece or the milling cutter itself, enabling the machine to access and mill complex angles and shapes that would be impossible with linear axes alone.
- Programming and Control:
The control unit within the CNC milling machine is programmed with the part's design and translated into G-code. This language specifies the position of the cutter and workpiece along the X, Y, and Z axes, as well as any rotational movements on the A, B, or C axes. The machine's control system reads these instructions and precisely controls the stepper motors or servo motors that drive the machine's movements.
The basic mechanics and coordinate systems of CNC milling machines are fundamental to their operation and capabilities. Understanding these principles is key to harnessing the full potential of CNC milling for efficient and precise part manufacturing.
Advantages of Computer Numeric Control (CNC) for Milling
- Precision and Repeatability
One of the key advantages of CNC milling is its ability to produce parts with extremely tight tolerances and consistent quality. This precision is crucial for parts that must fit together perfectly or function within narrow performance specifications.
- Enhanced Productivity and Efficiency
CNC milling allows for the automation of complex machining processes, significantly reducing the time from design to finished product. This leads to increased productivity and cost savings, as fewer manual operations are required.
- The Evolution of CNC Control: From Punch Cards to G-Code
The control of CNC machines has evolved from the early use of punched paper tape and cards to the modern use of G-code. This evolution has made programming more accessible and precise.
How CNC Milling Delivers Quality Parts
Multi-axis machining, as mentioned earlier, is the principle of CNC milling for precision machining, but how do they operate and process quality parts?
- Suitability for Non-Round and Asymmetrical Parts
CNC milling stands out for its ability to produce parts that deviate from the standard round or symmetrical shapes. The process is particularly adept at handling complex geometries, offering a high degree of accuracy that is essential for components with intricate designs.
This capability is invaluable in industries such as aerospace, medical, and automotive, where parts often have irregular shapes that are critical to their performance. The precision of CNC milling ensures that each part is manufactured to exact specifications, allowing for the creation of efficient and innovative designs that may offer improved functionality or reduced weight.
2. Creating Complex Shapes and Maintaining Precision
Multi-axis CNC milling, especially with 5-axis capabilities, allows for the creation of parts with complex shapes that would be unattainable on simpler machines. The additional axes enable the cutting tool to approach the workpiece from various angles, which not only facilitates the machining of complex geometries but also helps maintain precision.
This approach reduces the need for part repositioning, minimizing the potential for errors and damage. Furthermore, the ability to machine from multiple angles contributes to a consistent and high-quality surface finish, making multi-axis CNC milling a preferred choice for parts where precision and complexity are paramount.
Technical Insights: 3-Axis vs. 4-Axis vs. 5-Axis Machining
- 3-Axis Machiningis the most common and is suitable for prismatic parts.
- 4-Axis Machiningadds a rotational axis, allowing for more complex shapes.
- 5-Axis Machiningprovides the highest level of complexity, with two rotational axes for intricate part designs.
Advantages of Multi-Axis Machining
- Complex Shapes:Allows the creation of parts with complex geometries that would be unfeasible on simpler, 3-axis machines.
- Reduced Setups:Parts can be machined in various orientations from the same setup, reducing the need for repositioning and thus saving time.
- Improved Surface Finish:The ability to machine from different angles can lead to better surface finishes and reduced need for further finishing processes.
- Increased Material Removal Rates:Multi-axis machines can remove material more efficiently, leading to faster production times.
HordRT’s Custom CNC Milling Service
HordRT offers a comprehensive range of quick-turn CNC machining services tailored to meet the diverse needs of our clients. We deliver custom parts that are precise and produced with remarkable efficiency.
- Advanced Machining Centers: HordRT operates advanced 3-axis, 4-axis, and 5-axis CNC milling machines, ensuring that we can handle any complexity in design and production.
- Material Expertise: We work with a broad spectrum of materials, from standard metals like mild and stainless steel to exotic materials such as titanium, ensuring that your parts are manufactured from the most suitable material for their application.
- Quality Assurance: An incoming materials inspection lab equipped with sophisticated analytic testing instruments using Raman spectroscopy guarantees that all raw materials meet the highest standards before production begins.
At HordRT, we are dedicated to providing high-quality parts in a short time frame. Our goal is to be a reliable partner in your manufacturing journey, from initial concept to final product realization.
Conclusion
In conclusion, CNC milling is a versatile and indispensable tool in the manufacturing industry. It offers numerous benefits, including precision, repeatability, and enhanced productivity. HordRT's CNC milling service leverages these advantages to provide our clients with parts and prototypes that are second to none in terms of speed, precision, and flexibility.
Whether you need a complex part for a critical application or a custom prototype for a new invention, HordRT is here to deliver. Contact us today to learn more about how our CNC milling services can bring your manufacturing projects to life.