Contents
Die casting is a popular manufacturing process used to produce complex metal parts with high precision and efficiency. However, like any manufacturing method. it is prone to defects that can affect the quality, performance, and cost-effectiveness of the finished product. Identifying and understanding these defects, along with their causes and solutions, is essential for achieving high-quality die-cast components.
This article explores the most common defects in die casting, their root causes, and practical ways to prevent and fix them.
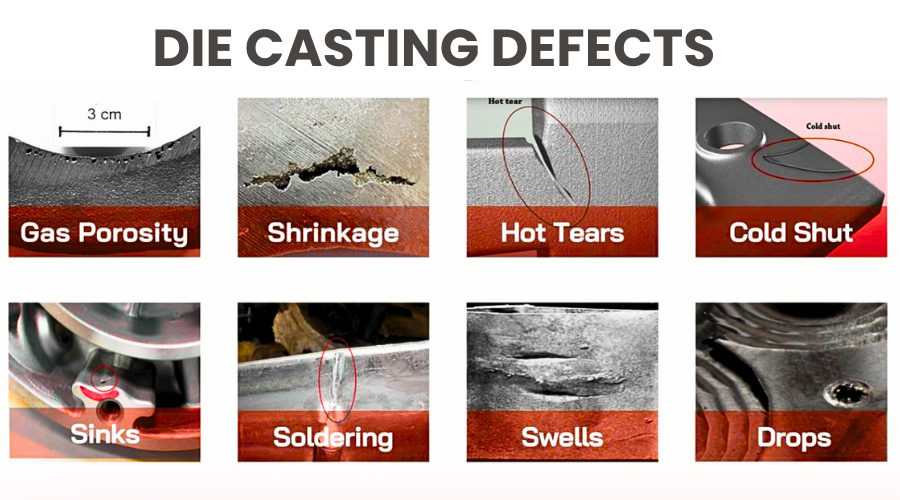
1. Porosity
Porosity is one of the most frequent issues encountered in die-casting. It refers to the presence of small holes or voids within the metal, which can weaken the part and reduce its structural integrity. There are two primary types of porosity in die-casting.
- Gas Porosity: Caused by trapped air or gases during the casting process.
- Shrinkage Porosity: This occurs when the metal shrinks as it cools, leaving voids or gaps in the casting.
Causes:
- Gas Porosity: Entrapped air or gas in the molten metal, poor venting, or excessive lubricant use can cause gas porosity. Additionally, turbulence during metal flow can trap gases in the casting.
- Shrinkage Porosity: Uneven cooling of the casting can lead to shrinkage porosity, especially in areas where the metal is thick or slow to cool.
Prevention:
- Optimize Gate and Venting Design: Proper gate placement and adequate venting allow gases to escape during the casting process, preventing gas porosity.
- Control Metal Flow: Minimizing turbulence during the injection of molten metal into the die helps reduce the likelihood of entrapped gases. Use smooth flow channels and a slow fill rate if necessary.
- Proper Lubricant Application: Excessive use of die lubricants can cause vaporization, leading to gas entrapment.
- Use Vacuum-Assisted Casting: Vacuum systems can help remove trapped air and gases during the casting process, reducing gas porosity.
- Ensure Uniform Cooling: To prevent shrinkage porosity, focus on consistent cooling, particularly in thick sections of the casting.
Fixes:
- Impregnation: In cases where porosity is unavoidable, especially in pressure-critical parts, vacuum impregnating can be used to seal the pores by filling them with a resin or sealant.
- Machining: Minor porosity can sometimes be removed through post-casting machining, though this can add costs and may not always be feasible for complex parts.
2. Cold Shuts
Cold shuts occur when two or more streams of molten metal fail to merge properly during the casting process, leaving a visible line or weak area in the part. These defects can compromise the part's strength and appearance.
Causes:
- Low Temperature: If the molten metal cools too quickly before it fully fills the mold, it can cause cold shuts. This often happens when the die temperature is too low, or the molten metal itself is not heated enough.
- Inadequate Flow: Insufficient pressure during injection or improper gate design can lead to slow or uneven metal flow, increasing the risk of cold shuts.
Prevention:
- Increase Metal Temperature: Ensure the molten metal is at the correct temperature before injection. This helps the metal flow smoothly and completely fill the mold before solidifying.
- Maintain Die Temperature: Keep the die at an optimal temperature to prevent premature cooling of the molten metal. Preheating the die before casting is essential, especially for large or complex parts.
- Optimize Gate and Runner Design: Proper placement and sizing of gates and runners ensure a smooth and consistent flow of molten metal into the die cavity, reducing the risk of cold shuts.
- Increase Injection Speed: Higher injection speeds can help ensure that the molten metal fills the mold quickly and evenly, minimizing the chances of cold shuts forming.
Fixes:
- Welding: Cold shuts can sometimes be repaired by welding over the affected area, though this is not always an ideal solution, particularly for high-precision parts.
- Recasting: In most cases, recasting the part with the necessary adjustments in temperature, flow, or gate design is the best way to eliminate cold shuts.
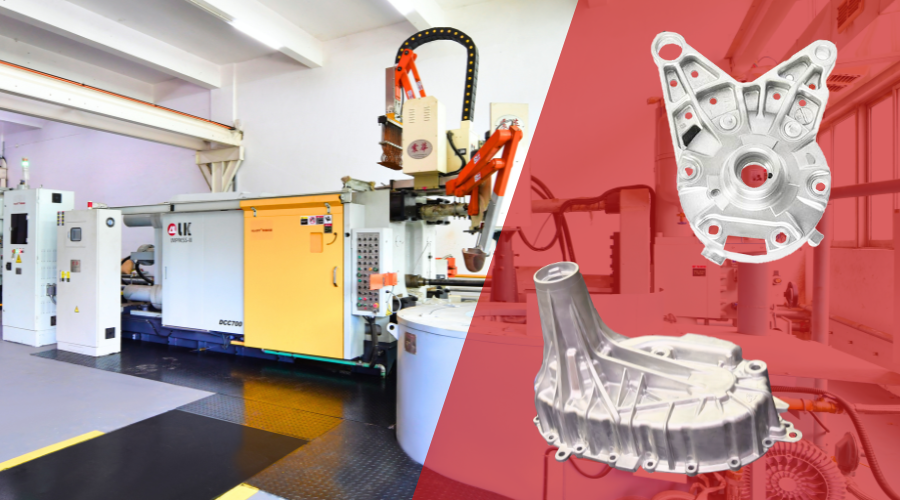
3. Flash
Flash occurs when excess molten metal escapes from the die and forms thin, unwanted material along the parting line or around holes. Although flash is usually removed during post-processing, excessive flash can lead to unnecessary waste and increased production costs.
Causes:
- Excessive Metal Pressure: If too much pressure is applied during the injection process, the molten metal may force its way out through gaps in the die, causing a flash.
- Die Wear: Worn-out dies with poorly fitting parts or gaps can allow molten metal to leak out during casting, leading to flash formation.
- Insufficient Clamping Force: When the die is not clamped tightly enough, the molten metal can seep through the parting lines.
Prevention:
- Maintain Proper Injection Pressure: Use the correct pressure for the casting process. Excessive pressure can cause flash, so adjust the injection force to prevent metal from escaping through die gaps.
- Inspect and Maintain Dies: Regularly inspect dies for signs of wear or damage. Repair or replace worn-out dies to ensure a tight seal during casting.
- Ensure Proper Clamping Force: Apply sufficient force to keep the die halves tightly together, preventing molten metal from escaping through the parting line.
Fixes:
- Deburring: Flash can often be removed through mechanical deburring or trimming, but this adds extra cost and time to the production process.
- Die Maintenance: If the die is worn, it should be repaired or replaced to prevent further occurrence of flash.
4. Misruns
A misrun occurs when the molten metal does not completely fill the mold, resulting in an incomplete part. Misruns can leave unfilled sections or thin, weak areas in the casting.
Causes:
- Low Metal Temperature: If the molten cools too quickly, it may solidify before it has completely filled the mold.
- Inadequate Pressure: Low injection pressure can cause the metal to flow too slowly, leading to incomplete filling of the die cavity.
- Complex Geometry: Parts with intricate designs or thin sections are more prone to misruns because they require more precise metal flow.
Prevention
- Increase Metal Temperature: Ensure the molten metal is at the appropriate temperature solidification during the casting process.
- Optimize Injection Pressure: Adjust the injection pressure to ensure that the molten metal flows quickly and fully fills the mold before cooling.
- Modify Die Design: Simplifying complex designs or adding flow channels can improve metal flow and prevent misruns in difficult-to-fill areas.
Fixes:
- Recasting: Misruns usually require recasting with adjustments to temperature, pressure, or design to ensure complete mold filling.
- Machining: In some cases, post-casting machining can remove incomplete sections, but this is often limited by the severity of the misrun.
5. Soldering (Sticking)
Soldering, or sticking, occurs when the molten metal adheres to the surface of the die, making it difficult to remove the part from the die and causing surface imperfections.
Causes:
- High Metal Temperature: When the molten is too hot, it can bond with the die surface, leading to soldering.
- Poor Die Lubrication: Inadequate application of die release agents can increase friction between the metal and the die, causing sticking.
- Die Material: Certain die materials may be more prone to sticking, particularly when casting metals like aluminum, which can chemically bond with the die surface.
Prevention:
- Control Metal Temperature: Ensure the molten metal is at the correct temperature to prevent it from bonding with the die surface.
- Use Release Agents: Apply sufficient die lubricants or release agents to prevent soldering. Be careful not to overuse lubricants, as this can lead to other defects like gas porosity.
- Coating the Die: Applying a protective coating to the die can prevent the molten metal from bonding with the die surface.
Fixes:
- Polishing: Sticking can cause surface defects, which may be fixed through polishing or other surface finishing techniques.
- Coating or Die Replacement: In severe cases, the die may need to be recoated or replaced if soldering has caused damage.
6. Hot Cracking
Hot cracking, also known as hot tearing, occurs when the metal contracts during the cooling phase, causing cracks to appear in the part. This typically happens in areas with high stress or non-uniform cooling rates.
Causes:
- Non-Uniform Cooling: Parts with thick sections or inconsistent cooling rates are more prone to hot cracking.
- Excessive Shrinkage Stress: If the metal contacts too quickly or unevenly, it can create stress points that lead to cracking.
- Improper Die Design: Complex geometries or sharp corners can concentrate stress, making hot cracking more likely.
Prevention:
- Control Cooling Rate: Use cooling systems in the die or apply external cooling to ensure uniform cooling across the entire part.
- Avoid Sharp Corners: Add fillets or round edges to reduce stress concentrations that could lead to cracking.
- Use Proper Alloys: Some alloys are more resistant to cracking than others. Choosing the right material for the part and process can help minimize hot cracking.
Fixes:
- Redesign the Part: Reducing sharp corners or adding stress-relief features like fillets can help prevent cracking in future castings.
- Post-Casting Repair: For small cracks, welding or brazing can be used to repair the affected areas, though this may compromise part integrity.
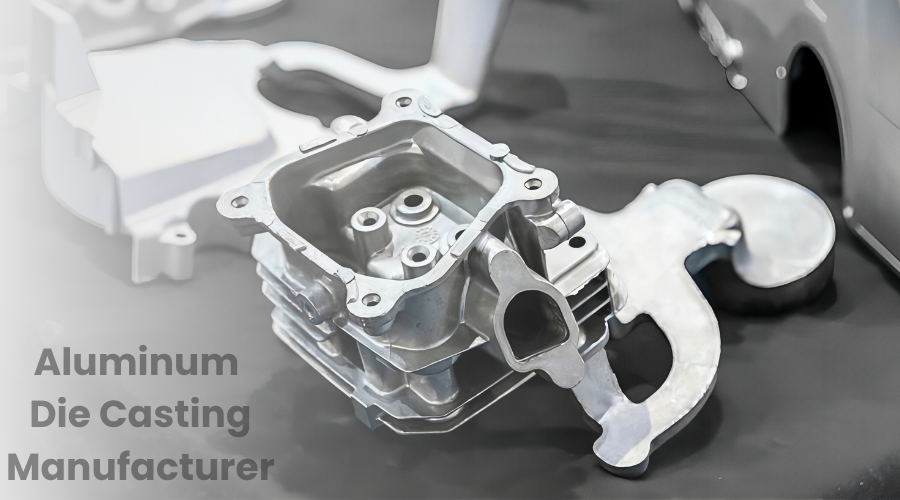
7. Sink Marks
Sink marks are depressions or indentations that appear on the surface of the part, usually caused by uneven cooling or insufficient material in certain areas. These can affect the part's appearance and mechanical properties.
Causes:
- Thick Section: Sink marks are more common in parts with thick sections, where the outer surface cools faster than the inner material.
- Insufficient Packing Pressure: Inadequate pressure during the cooling phase can allow the material to contract, leading to sink marks.
- Material Shrinkage: As the molten metal solidifies, it can shrink, leaving voids or depressions on the surface.
Prevention:
- Uniform Wall Thickness: Design the part with consistent wall thickness to ensure even cooling and avoid sink marks.
- Increase Packing Pressure: Apply more pressure during the cooling phase to ensure the material is properly packed and does not shrink excessively.
- Use Cooling Channels: Incorporate cooling channels to regulate the temperature and ensure uniform cooling throughout the part.
Fixes:
- Machining: Sink marks can sometimes be removed through post-casting machining, but this may increase production costs.
- Redesign the Part: Adjusting the design to eliminate thick sections or adding features like ribs can help prevent sink marks in future castings.
Conclusion
Understanding and addressing common defects in die casting is crucial for producing high-quality components efficiently. By recognizing the root causes of defects such as porosity, cold shuts, flashes, misruns, soldering, hot cracking, and sink marks, manufacturers can take proactive steps to prevent and fix these issues. Solutions like optimizing gate design, controlling cooling rates, adjusting metal temperatures, and maintaining die integrity are essential for enhancing the quality and cost-effectiveness of the die-casting process. Implementing these best practices not only ensures better part performance but also reduces wastage and production costs, making the entire process more reliable and sustainable.