High-quality surface finishing services improve your part’s aesthetics and functions regardless of the manufacturing process used. Deliver quality metal, composites, and plastic finishing services so you can bring the prototype or part you dream of to life.
What is Surface Finishing
Surface finishing refers to any process used to modify the surface of a material to improve its appearance or performance. Surface finishing can involve mechanical processes, such as polishing or grinding, chemical processes, such as plating or anodizing, or other methods such as painting or coating.
The purpose of surface finishing may be to increase durability, improve corrosion resistance, enhance electrical conductivity, or simply provide a better aesthetic appearance. Surface finishing can be applied to a wide range of materials including metals, plastics, ceramics, and composites.
In summary, surface finishing is a set of techniques used to modify the surface of a material to improve its properties and/or appearance.

The Benefits of Surface Finishing
Surface finishing refers to the process of modifying the surface of a material to improve its appearance, durability, and functionality. There are several benefits of surface finishing, including:
Enhanced appearance: Surface finishing can improve the aesthetics of a material by providing a smooth, glossy, or textured finish. This can be particularly important in industries where visual appeal is critical, such as in the automotive or consumer goods industries.
Improved durability: Surface finishing can improve the material's resistance to wear and tear, corrosion, and other forms of damage. This can extend the lifespan of the material and reduce the need for costly repairs or replacements.
Increased functionality: Surface finishing can add new functionality to a material, such as anti-slip properties or electrical conductivity. This can broaden the range of applications for the material and increase its value.
Protection: Surface finishing can provide a protective layer against environmental factors such as UV rays, moisture, and chemicals. This can prevent damage to the material and prolong its lifespan.
Health and safety: Surface finishing can improve the safety and health of users by reducing sharp edges or preventing the growth of bacteria on surfaces.
Overall, surface finishing can provide significant benefits to materials across various industries and applications, improving their appearance, durability, functionality, and safety.
Types of Surface Finishing
Sure, there are many types of surface finishes used in various industries, here are some common types:
Polished Finish: A glossy and reflective finish achieved by smoothing a surface using abrasives such as sandpaper or polishing compounds.
Matte Finish: A non-reflective, flat finish that can be achieved by sandblasting, etching, or chemical treatment.
Brushed Finish: A textured finish created by brushing a surface with a wire brush or other abrasive material.
Satin Finish: A smooth and silky finish that is not as glossy as a polished finish but has a slight sheen. It can be achieved using abrasive pads or polishing compounds.
Anodized Finish: An electrolytic process that creates a protective coating on metal surfaces, often used in the aerospace and automotive industries.
Powder Coated Finish: A type of coating applied as a free-flowing dry powder, which is then cured under heat, resulting in a hard, durable finish.
Galvanized Finish: A process of applying a protective coating of zinc to metal surfaces to prevent rust and corrosion.
Textured Finish: A decorative finish that can be created by adding texture to a surface, such as by embossing, engraving, or applying a textured coating.
These are just a few examples of the many different types of surface finishes available, and the appropriate finish will depend on the application and desired aesthetic.
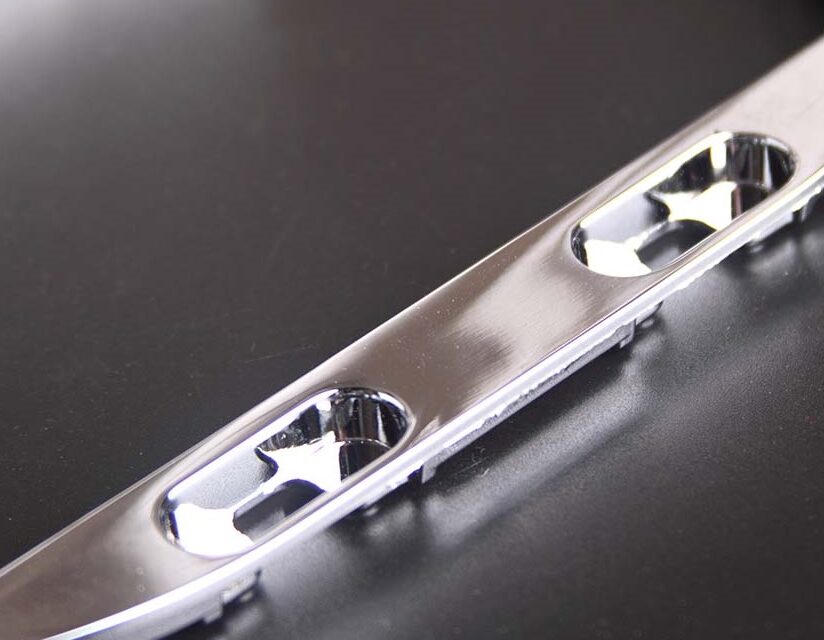
How to Choose Surface Finishing
The choice of surface finish will depend on various factors such as the material being used, the intended function of the object, and the desired aesthetic.
Here are some factors to consider when choosing a surface finish:
Material: The surface finish should be compatible with the material being used. For example, a polished finish may work well on metal surfaces, but may not be suitable for wood.
Function: The intended function of the object should also be taken into account. For example, a textured finish may be preferred for surfaces that require a non-slip grip, while a polished finish may be more appropriate for decorative objects.
Environment: The environment in which the object will be used should also be considered. For example, a galvanized finish may be necessary for metal objects that will be exposed to corrosive environments.
Maintenance: The maintenance requirements of the surface finish should also be taken into account. For example, a polished finish may require regular upkeep to maintain its appearance.
Aesthetics: Finally, the desired aesthetic effect should also be considered when choosing a surface finish. This may be a personal preference or may be dictated by the intended use of the object.
Overall, the choice of surface finish should be based on careful consideration of these various factors to ensure that the finish is both functional and aesthetically pleasing.