Injection molding is a widely used manufacturing process for producing plastic components with precision and efficiency. One critical aspect of this process is the strategic placement of cores and cavities within the mold. In this article, we will delve into the key considerations and factors that influence the decision-making process for core and cavity placement.
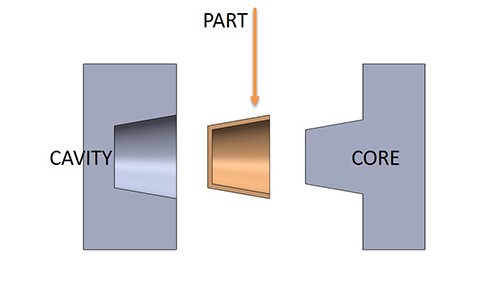
What are Cores and Cavities
Before we dive into the intricacies of core and cavity placement, it’s essential to understand the basic components. Cores and cavities are essential components of the mold that work together to form the final shape of a plastic part. Here’s a brief explanation of each.
1. Cores
- Cores are the internal components of the mold that shape the internal features of the plastic part.
- They create voids or negative space within the molded part.
- The molten plastic material is injected around the cores to form the internal geometry of the finished product.
- Cores are typically used to shape complex features such as holes, hollow sections, and other internal details of the part.
2. Cavities
- Cavities are the external components of the mold that shape the outer surface of the plastic part.
- They form the positive shape of the final product and determine the part’s external appearance.
- The molten plastic material fills the cavities, taking on their shape to produce the external features of the molded part.
- Cavities are responsible for creating the overall shape, texture, and surface finish of the finished product.
What Affects Core and Cavity Placement
Several factors influence the decision on where to place cores and cavities in the injection molding process:
1. Part Design: The design of the plastic component itself plays a crucial role in determining core and cavity placement. Complex geometries and intricate features may require specific considerations.
2. Material Properties: Different plastic materials exhibit unique behaviors during the molding process. Factors such as shrinkage, cooling rates, and flow characteristics can impact the optimal placement of cores and cavities.
3. Injection Molding Machine Capability: The specifications of the injection molding machine, including its tonnage and clamping force, influence the size and complexity of molds. These, in turn, affect the placement of cores and cavities.
4. Cooling Requirements: Efficient cooling is vital in injection molding to ensure proper solidification of the plastic material. Considerations for cooling channel placement and heat dissipation can impact the positioning of cores and cavities.
Core and Cavity Placement Considerations
When deciding on the placement of cores and cavities, manufacturers must consider the following factors:
1. Symmetry: Achieving symmetry in the mold design helps distribute forces evenly, minimizing the risk of warping and ensuring uniform part quality.
2. Gate Location: The location of the gate, where the molten plastic enters the mold, is crucial. Proper gate placement enhances flow characteristics and minimizes defects in the final product.
3. Wall Thickness: Maintaining consistent wall thickness is essential for preventing issues like sink marks and uneven cooling. Strategic core and cavity placement contribute to uniform wall thickness.
4. Ejection Mechanism: The design of the ejection system must be considered when determining core and cavity placement to ensure smooth and efficient removal of the molded part.
Summary
In conclusion, choosing the right core and cavity placement in injection molding is a multifaceted process that requires careful consideration of various factors. From part design and material properties to machine capabilities and cooling requirements, each element plays a crucial role in achieving optimal results. By understanding these considerations, manufacturers can enhance the efficiency, precision, and quality of their injection molding processes. Successful core and cavity placement ultimately contributes to the production of high-quality plastic components.