
Rapid tooling and low-volume production is our core business. We have been in this filed for many years and have the capability for all of customer manufacturing projects from prototyping to production.
Generally, we use P20 soft steel and hard aluminum 7075 or QC-10 to make rapid injection tooling, it is easier to make modification afterward. Here are the work procedure in Hord:
1.Once receiving the purchasing order, we will provide a design for manufacturing(DFM) review to confirm the parting line, gate size and position,ejector, draft, tolerance, wall thickness and warpage etc. Our engineer may come up with some suggestions. Customer need to confirm all the issues that will affect the appearance and function of the part.
2.The delivery time starts from the confirmation of DFM.
3.All incoming materials will be inspected. COA (Certificate of Analysis) of raw plastic material from our supplier would be provided.
4.Mold trial and dimensions report of T1 samples will be provided before shipment.
5.Tool tune or engineering changes requested by the customer.
After the final sample is approved, run the molding parts to finish the order. During the manufacturing process, our project engineer will double check the parts in terms of size, tolerance, and appearance.
For our rapid tooling, it usually takes about 2-3 weeks. If the project is urgent, we can finish the parts within 5-10 days based on different geometry, but there will be additional charge.
In order to make it faster and lower cost, we almost use the shared mold base(non-exported tool) unless other specification. All the shared mold base belong to Hord. If customer need to export the completed tooling, that is OK but cost will be high in this option.
If there is further more questions, please send email to rfq@hordrt.com. We will get back to you as soon as possible.
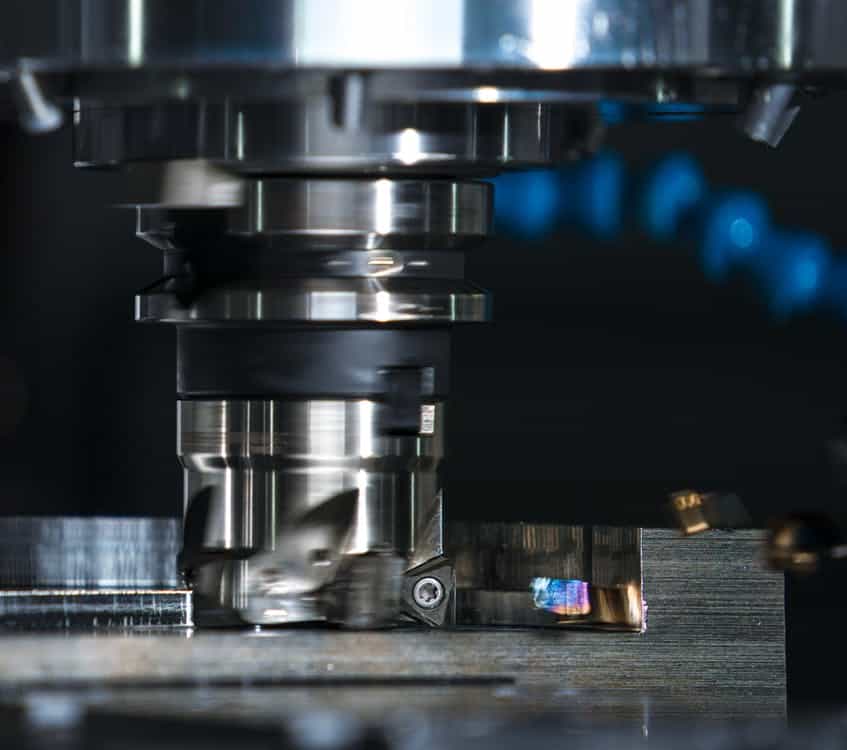
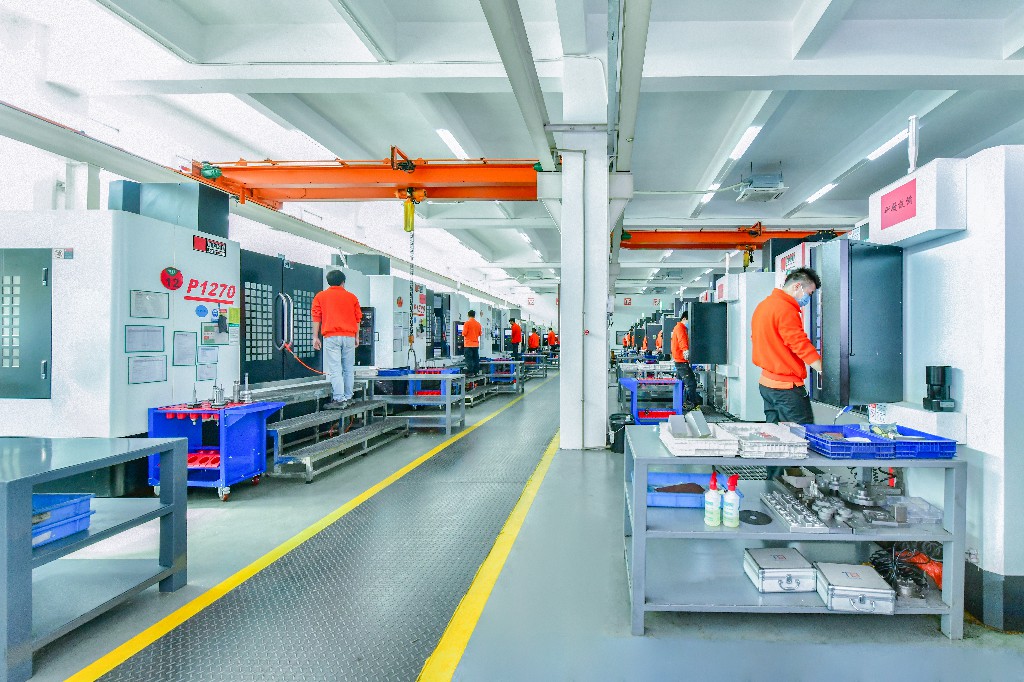