
Johnny Xiong
Rapid Tooling Expert
Contents
In today's fiercely competitive manufacturing environment, time-to-market has become a critical factor determining whether a company can seize market opportunities. To expedite product validation, testing, and small-batch production, more and more enterprises are turning to "rapid tooling" as an alternative to traditional tooling solutions. This article delves into the definition, processes, material selection, and technical advantages of rapid tooling.
1. What is Rapid Tooling?
Rapid tooling, also known as prototype tooling or bridge tooling, refers to a mold manufacturing method that is more cost-effective and has a shorter production cycle compared to traditional injection molds. It is typically used during the product development phase for functional validation, small-batch trials, or bridge production, assisting clients in completing product iterations and testing in a short time.
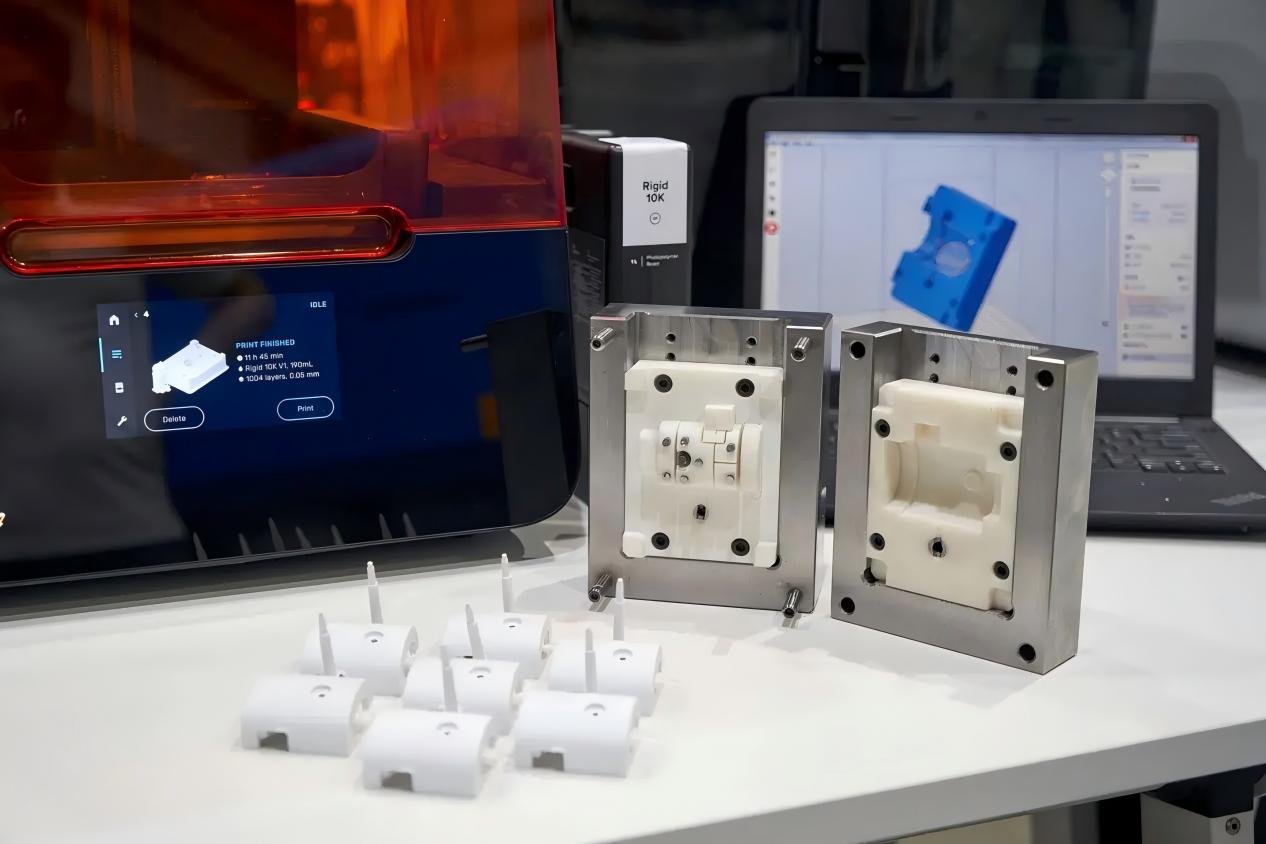
2. Rapid Tooling Manufacturing Process
The typical steps in rapid tooling production include:
- Product Design Confirmation: Evaluate manufacturability based on customer-provided 3D drawings and material requirements.
- Mold Structure Design:Design mold structures, considering technical details such as parting lines, draft angles, and venting.
- Mold Machining: Utilize CNC, EDM, and other machining methods to quickly complete mold core and base processing.
- Mold Assembly and Debugging: Assemble molds and conduct trial molding, optimizing injection parameters.
- Sample Trial and Optimization: Conduct small-batch trial production, inspect product appearance, dimensions, and performance, and make necessary mold adjustments.
Sample Confirmation and Delivery: After customer approval of samples, rapid tooling can continue to be used for small-batch production.
3. Common Materials
Since rapid tooling is generally used for small-batch production, material selection leans towards materials with fast machining speeds, lower costs, and moderate service life. Common mold materials include:
Material Type | Common Grades | Characteristics |
Aluminum Alloy | 7075, 6061 | Fast machining speed, good thermal conductivity, low cost |
Tool Steel | P20, NAK80 | Good wear resistance, suitable for medium-quantity trials |
Plastics | Epoxy resin, polyurethane | Often used for silicone molding, suitable for complex geometries |
4. Advantages of Rapid Tooling
- Shortened Development Cycle:Typically requires only 7–15 days to complete mold production, significantly saving early development time.
- Reduced Development Costs: Compared to traditional steel molds, costs are reduced by 30%–70%, suitable for budget-constrained startup projects.
- Facilitates Product Validation and Iteration:Convenient for design validation, functional testing, and structural optimization.
- Suitable for Small-Batch Production: Supports production volumes ranging from 10 to 5,000 pieces, meeting market testing and initial promotion needs.
- Lower Mass Production Risks:Validate product feasibility through small-batch molds before considering investment in formal molds.
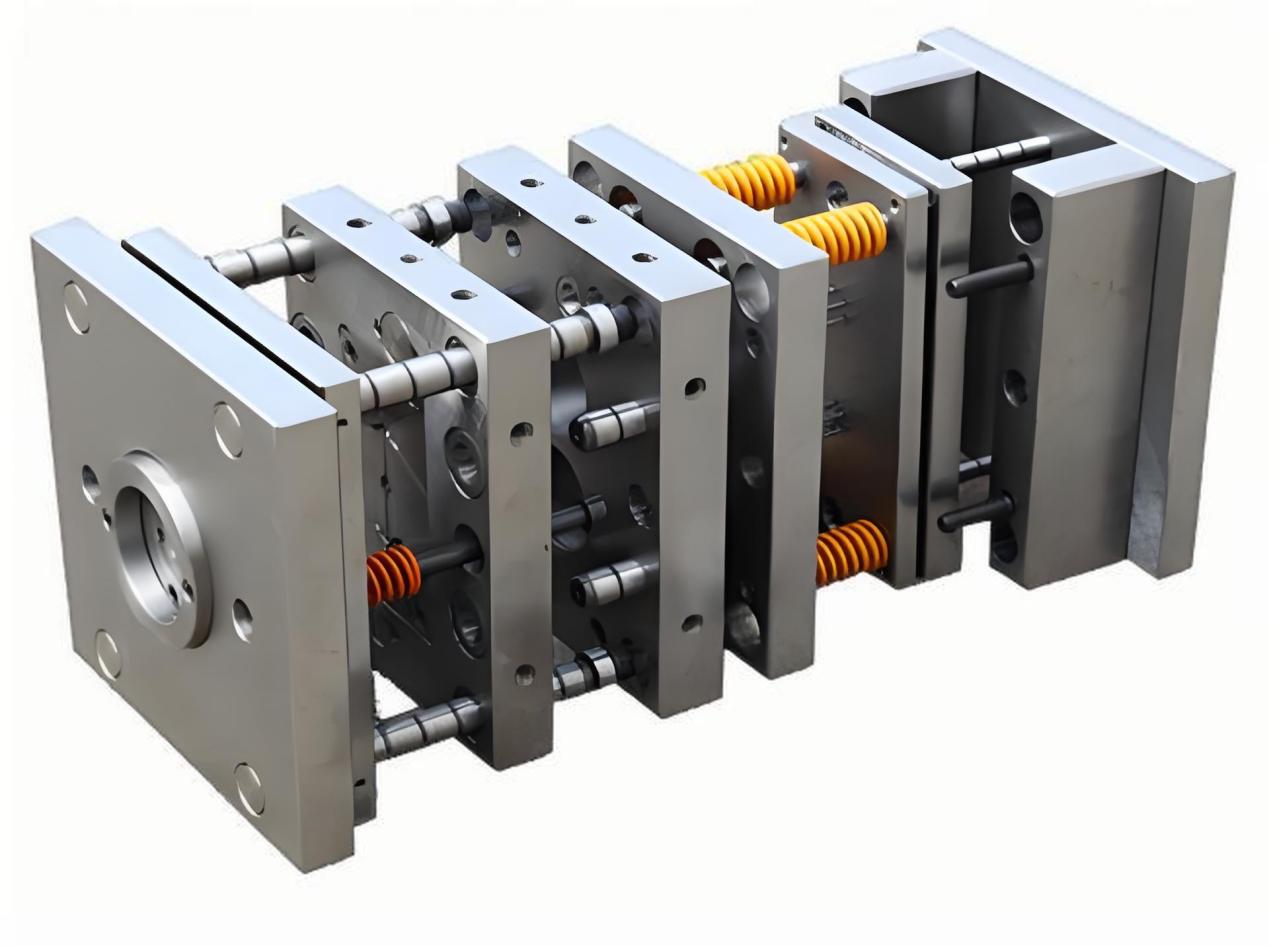
5. Rapid Tooling vs. Traditional Tooling
Item | Rapid Tooling | Traditional Tooling |
Production Cycle | 7–15 days | 30–60 days |
Production Cost | Lower | Higher |
Mold Lifespan | 5,000–10,000 cycles | 50,000–1,000,000+ cycles |
Suitable Production Volume | Small-batch, trials | Mass production |
Applicable Scenarios | Design validation, trial production, bridge production | Formal mass production |
Material Selection | Aluminum alloy, soft steel | Heat-treated steel |
6. Considerations and Limitations
Despite the numerous advantages of rapid tooling, attention should be paid to the following issues during use:
- Limited mold lifespan, not suitable for long-term use.
- Some complex structures or high-precision parts require more precise mold structure design.
- The surface quality of injection-molded products is closely related to mold materials and machining processes.
- Not suitable for high-gloss, transparent, or high-temperature molding materials (such as PMMA, PPS, etc.).
Therefore, before officially initiating a rapid tooling project, experienced engineers should conduct detailed evaluations and designs to ensure the optimization of the technical solution.
7. Future Trends in Aluminum Extrusion
As Industry 4.0 evolves, aluminum extrusion is becoming smarter and more sustainable:
- Intelligent extrusion lines: Automated control of temperature, speed, and pressure.
- Co-extrusion technology: Combines aluminum with plastic or copper for multi-functional parts.
- Eco-friendly materials: Greater use of recycled aluminum for sustainability.
- Complex profiles: Advanced dies produce intricate cross-sections for diverse applications.
Conclusion
Rapid tooling has become an efficient and flexible solution in modern manufacturing, particularly suitable for projects with tight product development cycles and strict cost control. It enables enterprises to complete structural validation, functional testing, and small-batch trials in a short time, serving as a key tool for agile development and rapid response to customer needs.
HordRT, as a professional custom tooling manufacturer in China, specializes in various processes such as rapid tooling, injection molding,CNC machining, and die casting, with extensive project experience and engineering support capabilities. If you have new product development, prototype trials, or bridge production needs, please contact us, and we will provide you with one-stop rapid manufacturing solutions.