
Johnny Xiong
Rapid Tooling Expert
Contents
Manufacturing relies on various technologies to create components that meet the demands of diverse industries. Among these, injection molding and extrusion stand out as versatile and widely-used methods. But how do these two processes differ, and when should each be chosen? This article explores their distinctions, advantages, disadvantages, and applications to help you make an informed decision for your project.
What is the Difference Between Injection Molding and Extrusion?
Injection molding and extrusion serve different purposes in manufacturing. Each method has its unique process, capabilities, and ideal use cases:
Injection Molding
Injection molding is designed to create complex, three-dimensional parts. It involves melting plastic material and injecting it into a mold, which defines the final shape. Once cooled and solidified, the part is ejected. This process is ideal for producing detailed, high-precision components.
Extrusion
Extrusion, on the other hand, focuses on creating continuous profiles with uniform cross-sections. In this process, molten material is forced through a die, resulting in long products like pipes, tubes, or sheets. The extruded material is cooled and cut to the desired length. This method excels at producing simple, continuous shapes efficiently.

What Are the Advantages and Disadvantages of Extrusion?
Let’s delve into why extrusion is valued for certain applications and where its limitations lie.
Advantages of Extrusion
- Continuous Production: Extrusion is highly efficient for manufacturing long parts with consistent cross-sections, such as plastic pipes and window frames.
- Low Tooling Costs: Compared to injection molding, extrusion has lower upfront costs, making it an economical choice for simpler profiles.
- Material Efficiency: The process minimizes material waste, contributing to cost savings and sustainability.
Disadvantages of Extrusion
- Limited Complexity: Extrusion is not suitable for parts with intricate geometries or high precision requirements.
- Surface Finish: Extruded parts may require secondary processing to achieve a smooth finish.
- Strength Variability: Depending on the material and design, structural strength may differ along the extrusion axis.
What Are the Advantages and Disadvantages of Injection Molding?
Injection molding offers significant advantages for specific manufacturing needs but also comes with challenges.
Advantages of Injection Molding
- Complex Geometry: Injection molding is unmatched in producing detailed 3D parts with tight tolerances.
- Scalability: It is cost-effective for large production runs, as the per-unit cost decreases significantly at scale.
- Material Versatility: A wide variety of materials can be used, allowing for tailored mechanical and thermal properties.
Disadvantages of Injection Molding
- High Initial Cost: Tooling and mold creation involve substantial upfront investment.
- Lead Time: Developing molds can take weeks, making the process less suitable for rapid prototyping.
- Small Batch Inefficiency: For low-volume production, the high setup costs make it less economical compared to extrusion or other methods.
How Do Injection Molding and Extrusion Compare in Detail?
To fully understand these methods, let’s compare them across key factors.
- Part Complexity
- Injection Molding: Capable of creating intricate designs, including parts with undercuts, holes, and textured surfaces.
- Extrusion: Limited to simple shapes with a uniform cross-section.
- Production Scale
- Injection Molding: Best suited for batch production of identical parts, especially at high volumes.
- Extrusion: Optimal for continuous production of long parts, such as tubing or profiles.
- Tooling Costs
- Injection Molding: High initial investment in molds, but cost-effective in the long term for large-scale production.
- Extrusion: Lower tooling costs, but limited in flexibility for design changes.
- Applications
- Injection Molding: Ideal for creating consumer goods, automotive components, and medical devices that require precision.
- Extrusion: Commonly used for manufacturing plastic pipes, window frames, and sheets that require uniformity.
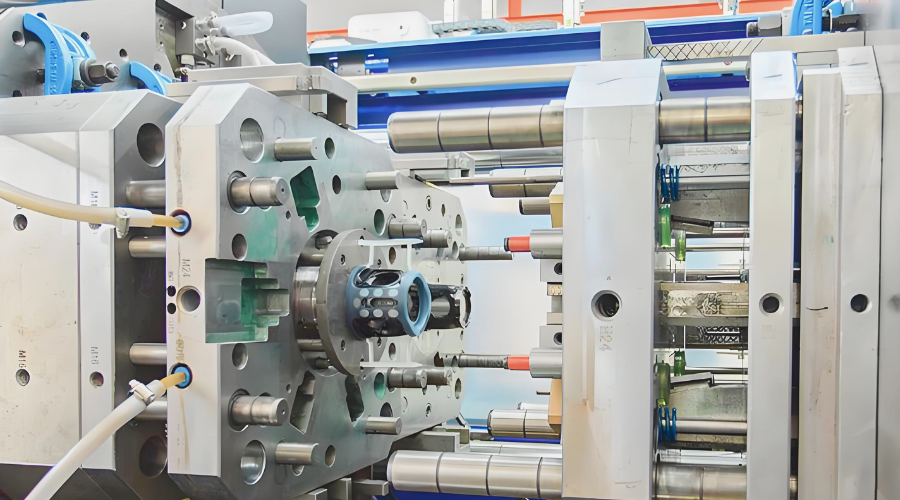
Conclusion
Both injection molding and extrusion play critical roles in manufacturing. While extrusion is highly efficient for producing long, continuous parts with simple profiles, injection molding excels at creating complex, high-precision components at scale.
For projects requiring intricate 3D designs, injection molding is the superior choice, especially when paired with large-scale production goals. However, if your needs involve straightforward, continuous shapes, extrusion may be more practical and cost-effective.
At HordRT, we specialize in injection molding, offering expertise and efficiency for producing high-quality parts tailored to your exact specifications. If you’re navigating the complexities of manufacturing decisions, our team is here to guide you toward the right solution.