
Johnny Xiong
Rapid Tooling Expert
Contents
Anodizing is an electrochemical surface treatment that forms a dense oxide layer on metal surfaces. Widely used in aerospace, automotive, electronics, and construction, this process significantly improves corrosion resistance, hardness, insulation, and aesthetics. This article presents a systematic overview of anodizing principles, process steps, common types, benefits, and real-world applications to help engineers and procurement teams fully understand this essential surface finishing technique.
1. How Anodizing Works
Anodizing involves an electrochemical reaction where the metal part serves as the anode in an electrolytic bath. Under direct current, a stable, tightly bonded oxide layer forms on the surface. This layer exhibits excellent physical and chemical properties and is resistant to peeling or chipping.
While various metals can be anodized (e.g., magnesium, titanium), aluminum and its alloys are most commonly used due to their transparency, hardness, and dyeability.
Typical electrolytes include sulfuric, oxalic, or chromic acid, selected based on desired coating properties.
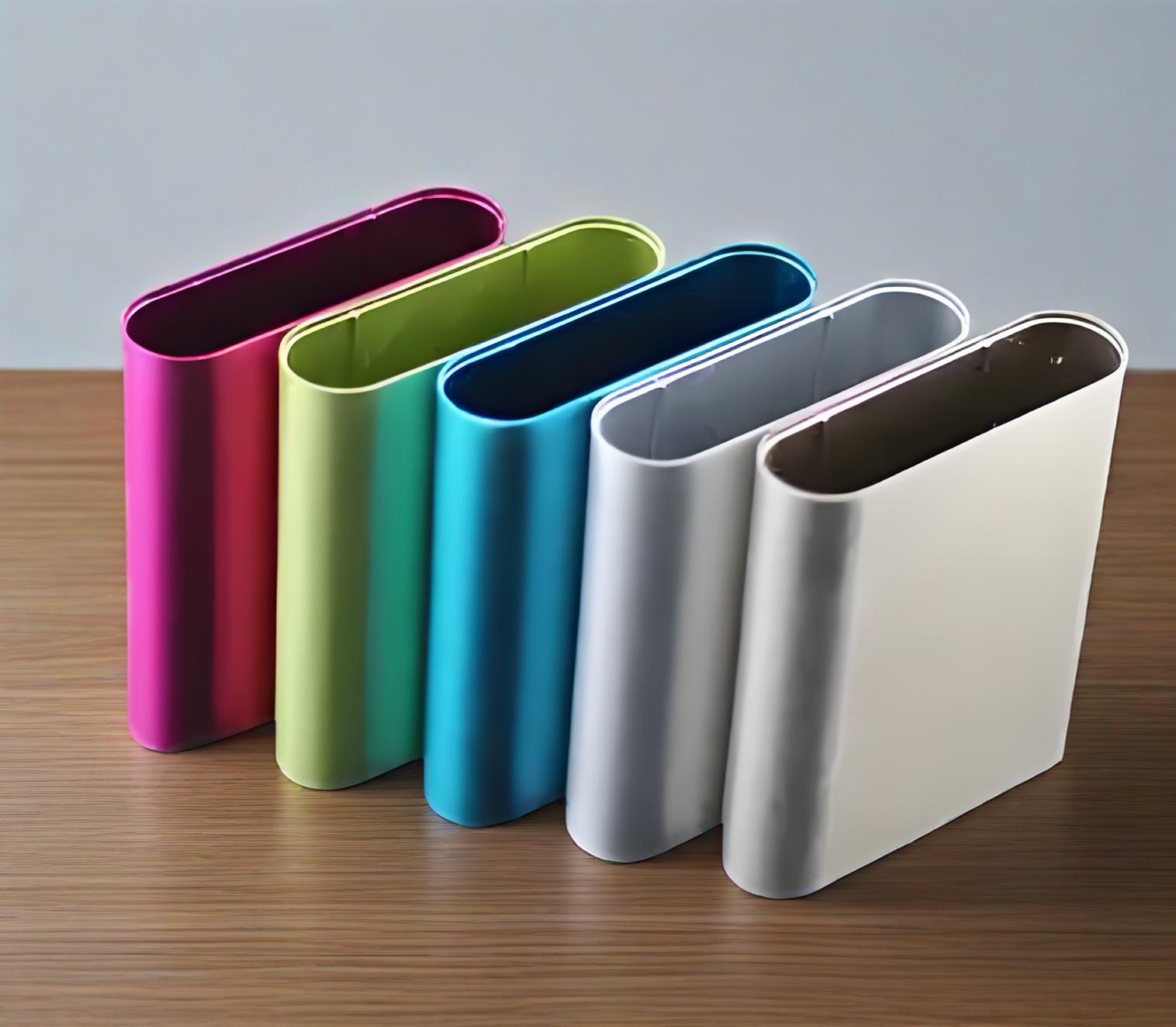
2. Anodizing Process Workflow
While specific steps may vary, the general process is as follows:
Step 1: Pre-treatment
- Degreasing → Rinsing → Chemical Cleaning (alkaline or acid) → Rinsing
- Purpose: Remove surface impurities to enhance film adhesion and uniformity
Step 2: Anodizing
- The part acts as the anode and is submerged in an electrolyte (e.g., sulfuric acid)
- Direct current is applied to generate the oxide layer
- Key parameters: voltage, current density, time, and temperature
Step 3: Coloring (Optional)
- The porous oxide layer can absorb dyes.
- Available in black, gold, bronze, red, and more, this step is often used in electronics and decorative applications.
Step 4: Sealing
- Micro-pores are sealed to enhance corrosion and stain resistance
- Common methods: hot water sealing, nickel salt sealing, cold sealing
Step 5: Drying and Inspection
- Dried parts are tested for appearance, coating thickness (measured in microns), hardness, adhesion, and color consistency
3. Types of Anodizing
Sulfuric Acid Anodizing (Type II)
- Moderate cost, good for coloring
- Thickness: 5–25 μm
- Used for decorative finishes, architectural aluminum, electronics casings
Hard Anodizing (Type III)
- Dense, highly durable, wear- and electrically-resistant
- Thickness: 25–150 μm
- Ideal for aerospace, defense, molds, and precision parts
Chromic Acid Anodizing
- Thin, flexible, resistant to cracking
- Thickness: 0.5–5 μm
- Used in riveted aircraft parts and adhesive bonding pre-treatment
Phosphoric Acid Anodizing
- Ultra-thin layer, enhances bonding strength
- Thickness: <1 μm
- Applied in aerospace composite bonding
4. Key Advantages of Anodizing
Corrosion Resistance
The oxide film acts as a barrier against moisture, salt, and chemical exposure, prolonging the life of the part.
Wear Resistance and Hardness
Particularly in hard anodizing, the coating can resist friction and abrasive wear, ideal for moving components.
Enhanced Aesthetic Appeal
The natural or dyed finishes improve product appearance and marketability, especially in consumer electronics.
Electrical Insulation
Anodized aluminum becomes non-conductive, suitable for high-voltage environments.
Improved Adhesion for Coatings and Adhesives
The porous layer enables better anchorage for paints, sealants, and bonding agents.
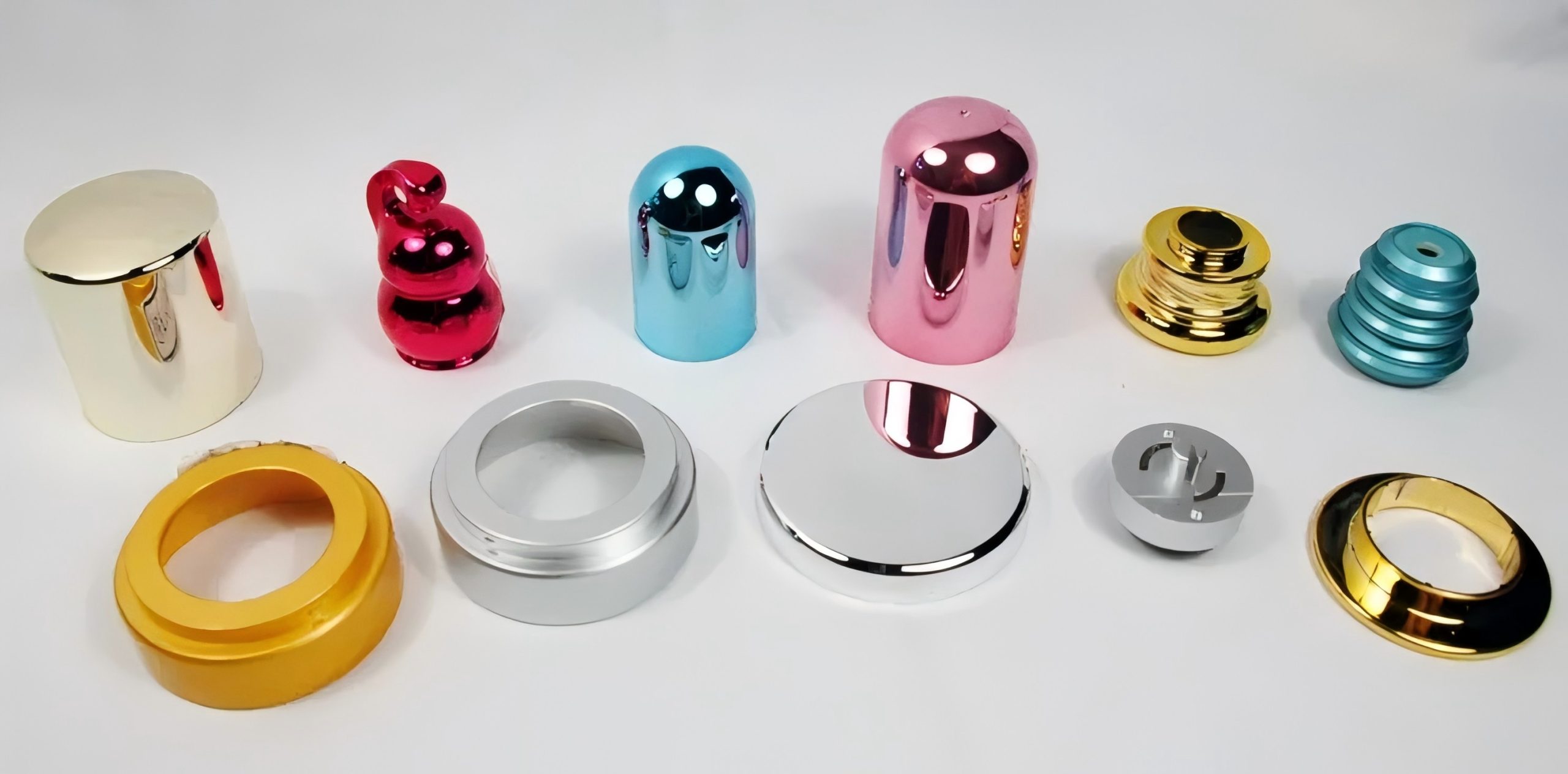
5. Typical Applications
- Aerospace:Aircraft skins, connectors, and structures requiring strength and corrosion resistance
- Consumer Electronics: Smartphone and laptop housings, speakers with stylish, scratch-resistant finishes
- Architecture: Aluminum doors, windows, curtain walls, and ceilings
- Automotive: Radiators, wheels, trim, and engine parts
- Machinery: Molds, fixtures, rails, and cylinders
6. Common Issues and Solutions
To ensure high-quality anodizing results:
- Choose appropriate alloys for anodizing
- Maintain thorough pre-treatment processes
- Precisely control current density, time, and temperature
- Measure film thickness, hardness, adhesion, and color consistency
- Selecting a supplier with experience and specialized anodizing lines is critical.
Conclusion
Anodizing is a reliable and efficient way to improve the performance, appearance, and longevity of aluminum components. As industries continue to demand higher standards, anodizing applications will keep expanding.
HordRT, a professional custom manufacturing company in China, offers one-stop solutions including CNC machining, plastic injection molding, aluminum die casting, silicone compression molding, sheet metal fabrication, and rapid tooling. With state-of-the-art facilities and strict quality control, we provide anodizing and other surface finishing services tailored to your needs.
Visit our website or contact our engineering team for technical support and customized service.