
Johnny Xiong
Rapid Tooling Expert
Contents
In modern manufacturing, aluminum extrusion has become a widely used processing technique due to its excellent plasticity, high strength-to-weight ratio, and corrosion resistance. It is extensively applied in aerospace, construction, automotive, electronics, electrical equipment, and rail transportation. This article explores the principles, processes, material selection, mold design, surface treatments, and common issues of aluminum extrusion, integrating HordRT’s professional experience to offer a practical and comprehensive technical reference.
1. Basic Principles of Aluminum Extrusion
Aluminum extrusion involves heating aluminum alloys to a suitable temperature and forcing them through a die to obtain the desired cross-sectional shape. It is essentially a form of plastic deformation.
Main process steps:
- Preheating the billet: Aluminum alloy billets are heated to 400–500°C to ensure good plasticity.
- Preheating the die: Dies are typically heated to around 450°C to avoid thermal shock and cracking.
- Extrusion forming: A hydraulic or mechanical press forces the heated billet through the die.
- Cooling and straightening: The extruded profile is cooled by air or water and then straightened.
- Cutting and aging: The profile is cut to length and artificially aged to enhance mechanical properties.
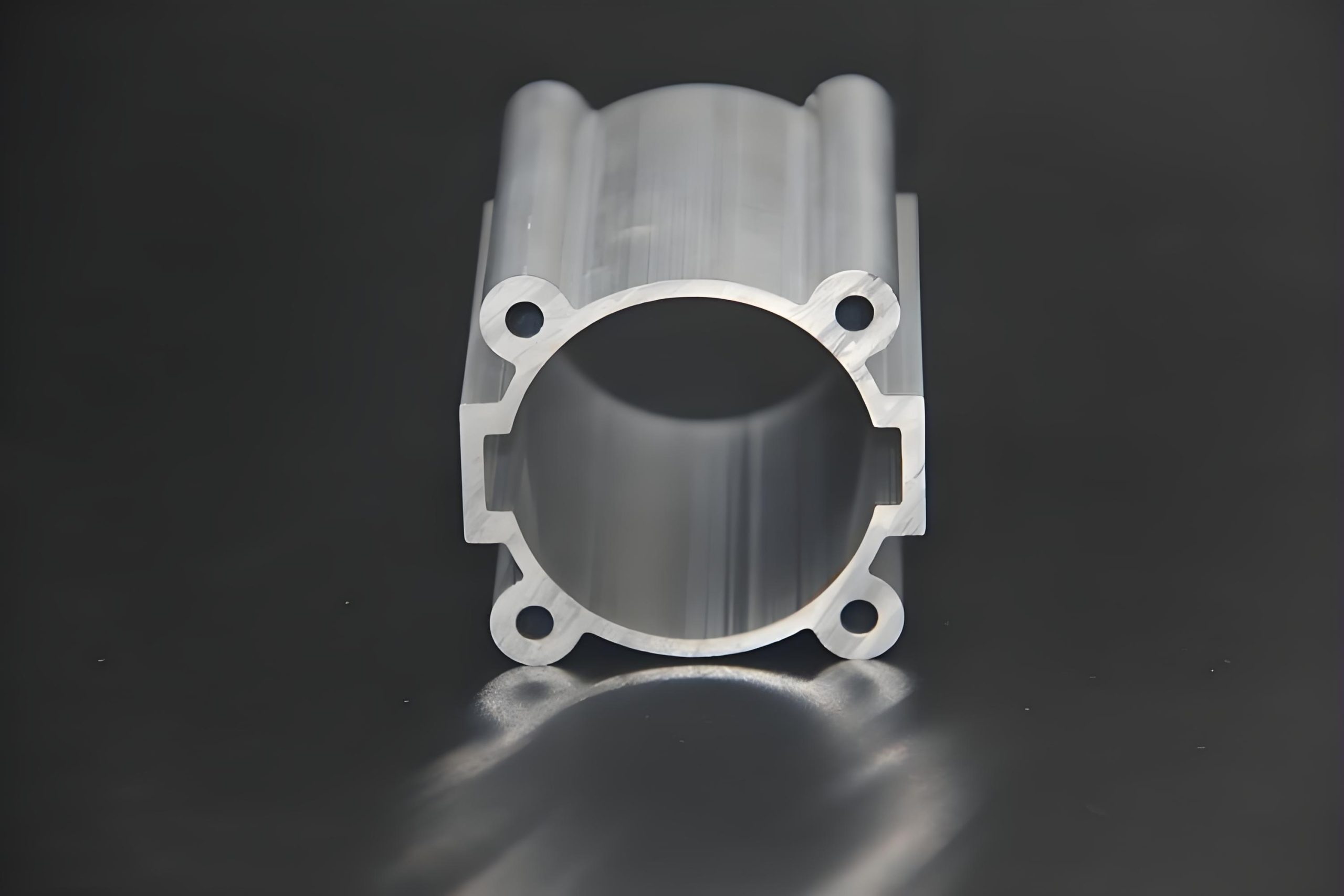
2. Common Aluminum Alloys and Their Properties
Material selection depends on application requirements. Below are typical alloy series:
Alloy Series | Grades | Key Properties | Applications |
6000 (Al-Mg-Si) | 6061, 6063 | High strength, corrosion-resistant, weldable, good machinability | Construction, transportation, industrial frames |
7000 (Al-Zn-Mg) | 7075 | Very high strength, excellent heat treatment response | Aerospace, military |
1000 (Pure Al) | 1050, 1060 | High plasticity, excellent conductivity, low strength | Electrical wires, capacitors, decoration |
3000 (Al-Mn) | 3003 | Good corrosion resistance, moderate strength | Roofing, kitchenware |
At HordRT, 6061 and 6063 are the most commonly used due to their well-rounded performance. We provide material recommendations and testing based on customer needs.
3. Key Points in Die Design
Dies play a crucial role in shaping and surface quality. A quality die should consider:
- Uniform metal flow: Optimized die openings ensure even flow and prevent twisting or waviness.
- Thermal stress resistance: Dies must resist thermal expansion and contraction to avoid cracking.
- Durability: Made from high-alloy tool steels (e.g., H13) and heat-treated for long service life.
HordRT uses 3D simulation and flow analysis during the design stage to ensure dimensional accuracy and durability.
4. Surface Treatment Methods for Aluminum Profiles
Although aluminum is naturally corrosion-resistant, further treatments enhance appearance and functionality:
- Anodizing: Forms a dense oxide layer, increasing hardness and corrosion resistance; available in various colors.
- Powder coating: Static electricity attaches paint powders for decorative and protective finishes.
- Electrophoresis coating: Produces uniform coatings in a conductive liquid; eco-friendly and durable.
- Polishing/brushing: Enhances visual appeal, often used for electronics or high-end products.
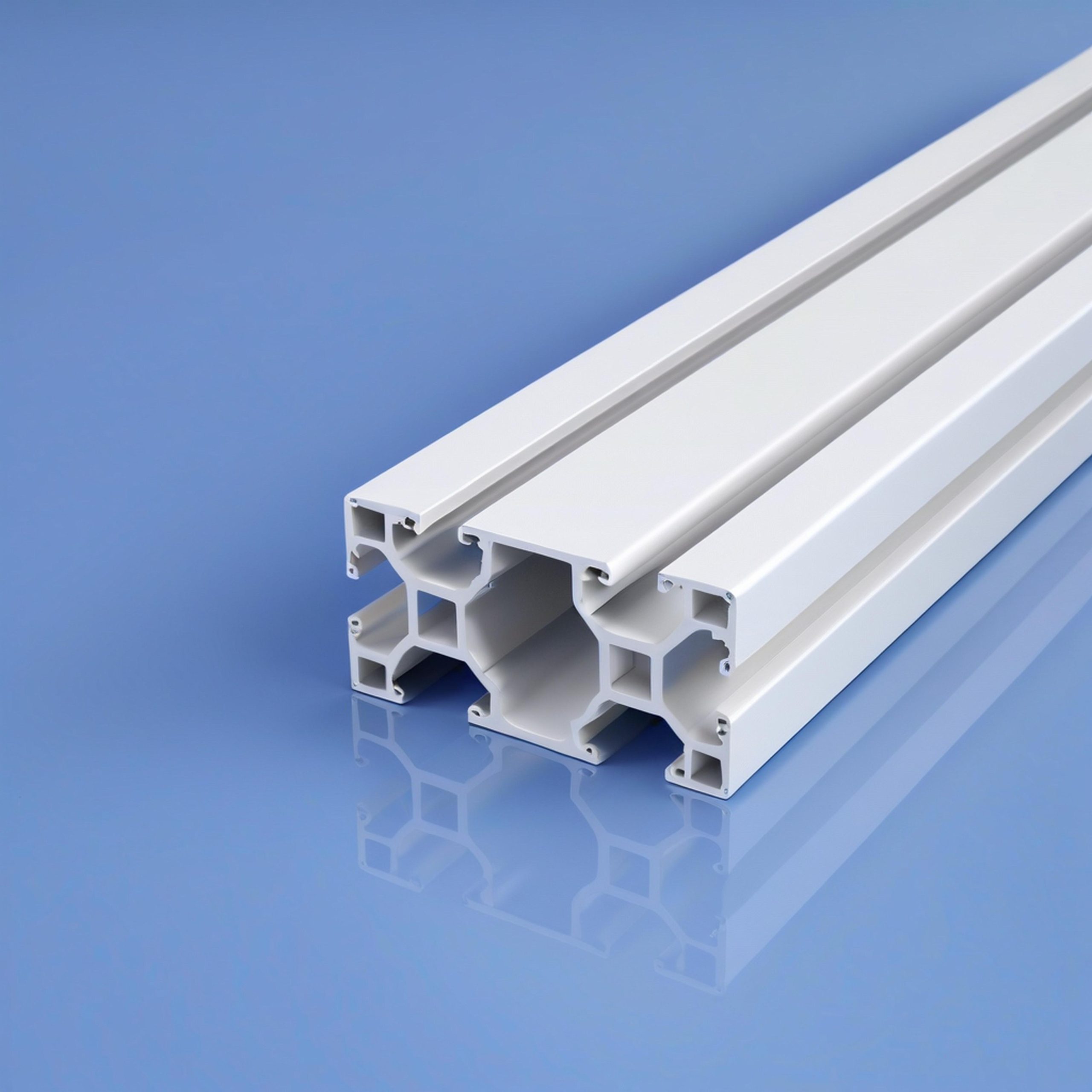
5. Precision Control in Aluminum Extrusion
Key metrics such as dimensional accuracy, straightness, and twist directly impact performance.
Influencing factors:
- Extrusion speed and temperature: Imbalances cause uneven metal flow.
- Die precision: Any die error transfers directly to the product.
- Stretching process: Improper handling can cause bending or warping.
- Heat treatment: Proper aging ensures consistent strength and accuracy.
6. Common Issues and Solutions
Issue | Possible Cause | Solution |
Surface scratches | Dirty equipment, damaged dies | Regular maintenance, optimize lubrication |
Dimensional error | Fluctuating speed or temperature | Optimize parameters, improve die accuracy |
Uneven anodizing | Surface contamination | Enhance cleaning, standardize processing |
Bubbles/inclusions | Impure raw materials | Use high-purity billets, degas before use |
7. Future Trends in Aluminum Extrusion
As Industry 4.0 evolves, aluminum extrusion is becoming smarter and more sustainable:
- Intelligent extrusion lines: Automated control of temperature, speed, and pressure.
- Co-extrusion technology: Combines aluminum with plastic or copper for multi-functional parts.
- Eco-friendly materials: Greater use of recycled aluminum for sustainability.
- Complex profiles: Advanced dies produce intricate cross-sections for diverse applications.
Conclusion
As a custom manufacturing specialist, HordRT provides not only aluminum extrusion but also CNC machining, anodizing, and assembly services—offering one-stop metal solutions. Whether for large-scale production or small-batch customization, we deliver cost-effective and high-quality results.
Looking for a reliable aluminum extrusion partner? Contact HordRT today and let’s innovate together!